Л. ТРОФИМОВ, канд. техн. наук, С. П. ГОРБУНОВ, Л. Я. КРАМАР, и Б. ЖУКОВ, инженеры (Челябинский политехнический ин-т, Использование отхода производства ферросилиция
При производстве ферросилиция на электрофильтрах улавливается тончайшая пыль, частицы которой имеют электростатический заряд, не уплотняются и загрязняют атмосферу. Выход этого проекта достигает нескольких десятков тонн в сутки, поэтому его утилизация весьма актуальна.
Диализ отхода на И К спектрофотометре «Спекорд» показал, что материал состоит, в основном, из стекловидного кремнезема типа обсидиана с небольшим количеством его водной аморфной разновидности, похожей на опал. По химическому и спектральному эмиссионному анализам содержание кремнезема достигает 98 %, оксидов железа и алюминия 1... 1,5 %, присутствуют также следы магния, натрия и др.
Дифференциально-термический анализ отхода выявил наличие экзотермических эффектов при 270 .. 280, 460 .. 470 и ",д)°С. Потери массы навески при нагреве до 1000°С составляют 1,5... 1,6%. Скорость изменения массы навески максимальна при 270 и 550°С. Полученные данные согласуются с результатами анализа в том, что основной составляющей отхода производства ферросилиция является безводный аморфный кремнезем. Он имеет плотность - 4 г/см3, насыпную плотность 0,2... П.3 г/см3, удельную площадь поверхности до 25000 см2/г.
Зерна отхода представляют собой высокопористые агрегаты аморфных округлых частиц размером менее 0,1 мкм. Подобный продукт известен за рубежом как силикатный дым или микрокремнезем.
В смеси с известью отход проявляет свойства активной минеральной добавки, связывая до 7% извести в низкоосновные гидросиликаты кальция за 5...7 ч нормального твердения при соотношении между известью и микрокремнеземом 1:1 по массе.
Высокая активность микрокремнезема позволяет использовать его в качестве добавки для повышения качества бетона и экономии цемента. В Челябинском политехническом институте исследовали его
влияние на некоторые свойства бетонной смеси и бетона. Введение добавки повышает водопотребность цементного теста на 1,41...1,46% массы цемента; удлиняются сроки схватывания вяжущего: начало схватывания на 11...13 мин, конец схватывания на 6...7 мин на каждый процент добавки.
Важнейшей задачей является разработка производственных способов транспортирования, складирования и дозирования микрокремнезема. На первом этапе разработана система приготовления суспензии, перевозки ее в автоцистернах н-объемного дозирования. Это позволяет использовать отходы в районе нх получения.
В бетонную смесь добавку вводили в виде водной суспензии, количество твердой фазы в единице объема которой определяли по формуле
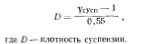
Влияние времени выдержки суспензии до ее введения в бетонную смесь на сохранение активности микрокремнезема изучали на образцах из цементного камня с В/Ц = 0,3, прочность которых определяли после тепловлажностной обработки по режиму 2+4+8+2 ч при температуре изотермической выдержки 85=С (табл 1).
Полученные результаты показали, что применение микрокремнезема в виде водной суспензии после различной выдержки способствует повышению прочности цементного камня.
Введение до 10% добавки снижает подвижность смеси на 2...3 см осадки конуса, при этом жесткость бетонной смеси практически не изменяется.
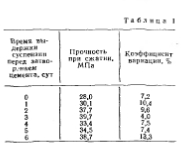
Для определения влияния количества добавки на прочность и морозостойкость бетона изготовляли образцы на портландцементе марки 400, гранодиоритовом щебне, кварцевом песке при соотношении компонентов 1:1,56:2,23:0,39 при расходе цемента 450 кг/м3. Прочность бетона определяли через 7 сут после ТВО, режим которой совпадал с режимом обработки цементного камня.
Введение 10% микрокремнезема позволяет почти пропорционально увеличить прочность бетона на сжатие на 1,2... 1,5 МПа на каждый процент добавки.
Морозостойкость бетона определяли ускоренным способом — замораживанием при —50СС образцов бетона в 5%-ном водном растворе хлорида натрия с последующим оттаиванием до +3—+5СС. Введение в бетонную смесь 8... 10% микрокремнезема повышает морозостойкость бетона в 2...3 раза.
Структурные особенности цементного камня с микрокремнеземом изучали с помощью термического анализа. Кривые ДТА, ДТГ и ТГ цементного камня с добавкой 9% микрокремнезема и цементного камня без добавок после ТВО приведены на рис.
Под влиянием добавки содержание гидроксида кальция в цементном камне уменьшается с 12 до 2,5%, а эндоэффект, характеризующий дегидратацию Са(ОН), смещается с 510 до 480°С, что позволяет предполагать меньшую степень закристаллизованности свободного гидроксида кальция. Эндоэффект при 660, 74 С и экзоэффект при 870°С указывают на повышенное количество низкоосновних гидросиликатов кальция типа С—S—Н(В) с различной степенью закристализованности в цементном камне с пылевидной добавкой. Количество химически связанной воды в цементном камне с добавкой микрокремнезема составляет 13,8% вместо 13,4% массы цемента в камне без добавки. При уменьшении содержания гидроксида кальция в 4,8 раза также резко увеличивается содержание низкоосновных гидросиликатов кальция.
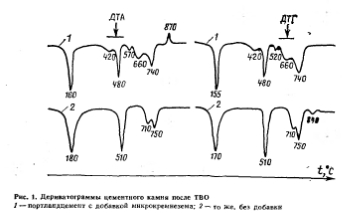
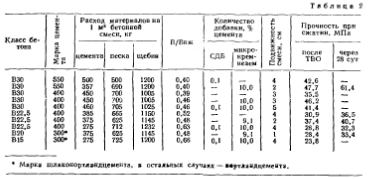
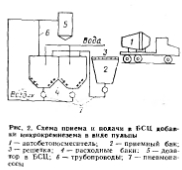
Пористость бетона определяли согласно ГОСТ 12730.4—78 по кинетике водопоглощения. Испытывали по 7 образцов бетона с добавкой 10% микрокремнезема и без него через 7 сут после ТВО по указанному выше режиму. Из расчетов, показателей пористости следует, что введение 10% микрокремнезема позволило почти в 3 раза уменьшить показатель среднего размера открытых капиллярных пор. Коэффициент вариации при определении водопоглощения составлял не более 5,6%, показатель однородности размера пор — 0,5.
Для повышения подвижности бетонной смеси в нее вводили до 0,8% С-3 или 0,15% СДБ. Бетон с добавкой суперпластификатора с В/Ц=0,25...0,3 после ТВО имеет прочность 45...50 МПа (на цементе марки 550), а введение дополнительно микрокремнезема повышает его прочность до 70...75 МПа и через 7 сут дополнительного нормального твердения— до 100 МПа. Повышенной прочности можно добиться и при использовании добав кв СДБ. Прочность бетона нормального твердения через 28 сут выше прочности бетона того же возраста, прошедшего ТВО, на 5—8%.
Учитывая особенности микрокремнезма, была разработана и осуществляет технология транспортирования и дозирования его в виде шлама. Добавку в автобетоносмесителях, загружают сухую пыль из бункерая пылеуловителя при одновременой подаче воды во вращающийся барабан автобетоиосмесителя. В результате образуется пульпа плотностью 11 1200 кг/м3. На бетонном заводе авт тоносмеситель разгружается в прием бак вместимостью 20 м3, из которого пуд пу перекачивают в два расходных вместимостью по 40 м3. Плотность доводят разбавлением водой до кг/м3. В баках барботируется сжаты воздух для предотвращения расслоения и оседания пульпы.
Принятая технология введения микрокремнезема надежна и обеспечивает стабильные свойства бетона. В 1986 г. было изготовлено 24 тыс. м3 сборного железобетона с этой добавкой, что обеспечило экономию цемента свыше 1300 т. Капитальные затраты составили около 30 тыс. р., срок окупаемости — 3 мес.
Выводы
Проведенные испытания и опыт внедрения микрокремнезема при изготовлении сборного железобетона показали наибольшую его эффективность при дозировке 8—10% массы вяжущего с использованием портландцементов. В этом случае прочность бетона повышается на 1,5... 2 марки, а при совместном использовании микрокремнезема с пластификаторами без изменения технологии изготовления сборного железобетона можно получить высокомарочные бетоны прочностью до 100 МПа. Введение микрокремнезема позволяет в 2...2,5 раза повысить морозостойкость бетона, увеличить его плотность и водонепроницаемость путем уменьшения размеров пор и увеличения количества гелевой структурной составляющей цементного камня. При его введении удается снизить расход цемента на 28—30%, а марочную прочность бетона обеспечить сразу после ТВО, что свидетельствует об имеющихся дополнительных резервах повышения эффективности. Ожидаемый экономический эффект от снижения расхода цемента составляет 0,7—3 р/м3 бетона.
Главным направлением использования микрокремнезема должно стать улучшение качества бетона в результате повышения его прочности, водонепроницаемости и морозостойкости.
Бетон и железобетон, 1987