В. В. АФАНАСЬЕВА, канд. техн. наук (Ростокинский з-д ЖБК) Опыт Ростокинского завода ЖБК по экономному расходованию цемента
На Ростокинском заводе ЖБК ДСК-1 Главмосстроя на протяжении многих лет проводится планомерная работа по снижению расхода цемента. В одиннадцатой пятилетке его сэкономлено 5300 т, за 6 мес 1986 г.— 1040 т. Эта экономия достигнута за счет целого ряда мероприятий: разработки прогрессивных, технически обоснованных норм расхода цемента; применения эффективных химических добавок; снижения отпускной прочности конструкций; улучшения приема и транспортирования цемента; применения статистического контроля прочности бетона; совершенствования дозирования составляющих бетона; увеличения длительности твердения бетона в предпраздничные и выходные дни; совершенствования составов бетонных смесей и режимов тепловой обработки; рационализаторских предложений рабочих и служащих завода.
Технические мероприятия, осуществляемые на заводе, охватывают все технологические переделы на пути цемента от вагона до получения готового изделия.
Большое внимание уделяется сокращению потерь цемента при разгрузке. Для этого внедрено пневмотранспортное оборудование, с помощью которого внутризаводские складские и транспортные потери вяжущего снижены до 1%. Применение пневмоавтоматики типа ЦИКЛ-БС при приготовлении бетонной смеси позволяет экономить до 0,5... 1% цемента при его дозировании.
На заводе проводится работа по уменьшению технологических потерь бетона за счет исключения плюсовых допусков при изготовлении железобетонных изделий. В результате, каждый год экономится не менее 100 т цемента. Столько же его экономится благодаря дополнительному выдерживанию изделий в пропарочных камерах в выходные и предпраздничные дни.
Большим резервом экономии цемента является совершенствование заводской технологии изготовления изделий. На одной из шаговых конвейерных линий внедрено новое устройство для уплотнения бетонных смесей — вибробрус, разработанный СПКТБ Кассетдеталь. Использование его вместо виброплощадки типа ВРА-15 позволяет сократить расход цемента на 25...30 кг/м3 за счет применения жестких бетонных смесей. Внедрение новых уплотняющих устройств намечено и на других конвейерных линиях.
Большое внимание уделяется совершенствованию тепловлажностной обработки изделий. Шаговые конвейерные линии оборудованы специальными щелевыми камерами. Для получения заданной отпускной прочности бетона с оптимальным расходом цемента применяются предварительно разогретые бетонные смеси с температурой до 45°С. Для создания влажной среды в камеры вмонтирована система форсунок для распыления влаги, замер температуры автоматизирован (одновременно замеряется температура в 9 точках камеры).
В целях совершенствования тепловой обработки кассетных машин применена оптимальная двухсторонняя схема теплоснабжения. Внесены изменения в режимы пропаривания: полностью исключена подача пара в течение изотермического прогрева. Пар подается в кассетные полости только в период подъема температуры. Общее время подачи пара в кассетные машины в основном не превышает 3 ч.
Одним из наиболее перспективных направлений экономии цемента является использование химических добавок. В последнее время в промышленности сборного железобетона расширяется применение высокоэффективных добавок — разжижителей бетонной смеси (С-3, 10-03), которые принято называть суперпластификаторами. Внедрение таких добавок позволяет без увеличения водосодержания получать либо литые бетонные смеси, не требующие интенсивной вибрации при формовании, либо за счет снижения водосодержания экономить до 20% цемента.
На Ростокинском заводе ЖБК совместно с НИИЖБом внедрен суперпластификатор С-3 для изготовления железобетонных изделий на конвейерных линиях. Опыт работы с ним показал. что введение его в бетонную смесь позволял ст увеличить подвижность с 8 до 23 см, уменьшить водосодержание бетонный смесей на 30%. Выявлено, что при одинаковом расходе цемента у исходно смеси и смеси с добавкой прочность оказывается на 20% выше у бетона с добавкой. Это позволяет экономить 12...15% цемента, или 50...70 кг/м3 пр уменьшенном В/Ц. При сохранении pat хода цемента добавка позволяет рабе тать с пластичными смесями более 15... 17 см вместо 8 см. что сокращает продолжительное формования в 1,5...2 раза и увеличивав оборачиваемость форм примерно на 30 При этом продолжительность тепловой обработки сокращается с 12 до 8 ч.
Практика показала, что добавку мод но эффективно использовать с учета конкретных технологических особенно стен изготовления изделий либо для формования по литьевой технологии, либо в целях экономии цемента. Можно использовать добавку одновременно с для некоторой экономии цемента, и для ускорения цикла формования, что в основном и делают на заводе. Формование железобетонных изделий на конвейерных линиях из более подвижных бетонных смесей (О.К.= 15...17 см вместо обычных 8 см) ускоряет ритм формования изделия почти в 2 раза, а число формовок увеличивается в 1,5 раза. При этом расход цемента сокращается на 30 40 кг/м3.
До недавнего времени считалось, что применение добавки С-3 в кассетной технологии ухудшает поверхность изделий: появляется большое по применению этой добавки Совместно с НИИЖБом были приведены соответствующие исследования г выявлена оптимальная подвижность бетонной смеси в интервале О.К.= 5...16 д:. установлен оптимальный расход для подвижных смесей, который равным 0.3...0,4% СУХОГО вещества от массы цемента. Превышение устав озленной дозировки для пластичных смесей приводит к снижению прочности бетона, ухудшению качества поверхности изделий.
Результаты работы показали целесообразность использования добавки в двух направлениях.
1. При сохранении обычных технологических параметров (температуры изотермического прогрева, подвижности и т р.) добавка позволяет снизить расход цемента до 70 кг/м3 (12...15%). но выливает ухудшение качества поверхности (больше пор, раковин).
2. При снижении температуры изотермического прогрева на 20°С(до 70°С) добавка позволяет на 40 кг/м3 снизить расход цемента. Качество поверхности изделий при этом не ухудшается. В процессе работы с добавкой выявлено так же ее положительное влияние на морозостойкость бетона. Установлено, что добавка С-3 вдвое увеличивает морозостойкость бетона, что дает возможность заводу изготовлять изделия с морозостойкостью 200 циклов и более без увеличения расхода цемента.
Для введения добавки в бетонную смесь заводом разработана, смонтирована и внедрена система хранения, транспортирования и дозирования добавки. Она включает емкости-цистерны; смеситель для приготовления рабочего состава заданной концентрации, расположенной в надбункерном отделении БСЦ; рабочую емкость для выдачи состава добавки в дозаторы, расположенную в дозаторном отделении.
За 1981—1985 гг. на заводе изготовлено более 400 тыс. м3 бетона с добавкой С-3, при этом сэкономлено 3000 т цемента.
Совместно с ВНИИЖелезобетоном для кассетной технологии заводчанами внедрена также химическая добавка ЛСТМ-2, представляющая собой технические модифицированные лигносульфонаты. Добавка позволяет пластифицировать бетонные смеси. Оптимальный расход ее составляет 0,1...0,15% в пересчете на сухое вещество от массы цемента. При одинаковом расходе цемента в исходной смеси и с добавкой прочность на 10...5°С выше у бетона с добавкой. Экономия цемента в лабораторных условиях составляет 10%, в производственных (с учетом неоднородности заполнителя). Большое влияние на расход цемента оказывает вид заполнителя: на щебне из плотных пород экономия цемента на 3 о выше, чем на щебне из известняковых пород. А поскольку завод вынужден работать на трех видах щебня, это "Питательно сказывается на обшей сумме экономии цемента за счет применения добавок.
Для введения ЛСТМ-2 в бетонную смесь разработана и смонтирована система хранения, транспортирования и Дозирования добавки. За 1984—1985 гг. на заводе изготовлено 150 тыс. м3 бетона с этой добавкой.
Контроль качества и его совершенствование в условиях завода способствуют осуществлению всех мероприятий по экономии цемента, улучшению качества продукции и уменьшению брака. Одним из наиболее существенных путей экономии цемента является статистический контроль прочности и однородности бетона по ГОСТ 18105.0—80 и ГОСТ 18105.1—80.
При статистическом контроле в случае достаточно высокой однородности бетона уменьшается значение требуемой (отпускной, передаточной и проектной) прочности бетона и представляется возможным соответственно снизить расход цемента. Применение статистического контроля предусматривает не только оценку результатов испытаний, но и регулирование прочности бетона с учетом требуемой прочности.
Для полного использования статистического метода контроля необходимо выполнение ряда технических мероприятий, способствующих повышению однородности бетона, — правильное складирование составляющих бетона, проверка дозировочного оборудования, контроль влажности песка, контроль режима тепловой обработки. Необходимо сохранять постоянство времени выдерживания отобранной пробы бетонной смеси до момента изготовления образцов и сроков испытаний их.
Внедрение статистического контроля даже при использовании трех видов рядовых заполнителей, перемешанных на складе, приводит к годовой экономии 80... 100 т цемента. При условии использования на заводе только одного вида заполнителя экономия цемента могла бы составить не менее 200 т в год.
Для предотвращения снижения прочности бетона или появления излишнего запаса прочности своевременно корректируется состав бетона или технологический режим производства. При работе на стабильных материалах общий коэффициент вариации находится в пределах 6. 9%. В целях обеспечения соответствия изделии технологическим требованиям установлена минимальная отпускная прочность изделий кассетного формования марки М200 в 12,5, марки М300 — в 18 МПа. Если статистический метод контроля позволяет иметь меньшую, чем указано выше, все расчеты ведутся по практически установленным безопасным величинам прочности.
Существенные резервы экономии цемента содержатся в правильном нормировании расхода цемента. На заводе он ограничивается производственными нормами, которые разрабатываются экспериментальным путем и проверяются в производственных условиях. Постоянно проводится работа по снижению норм расхода цемента. За счет пересмотра производственных норм за 1984—1985 гг. сэкономлено 1 032 т цемента. Однако существует ряд причин, которые приводят к повышенному расходу цемента на заводе. Основными являются поставка слабого известнякового щебня и портландцемента марки 500 вместо 400 (цемент имеет пониженную удельную поверхность и не всегда обеспечена его активность); создавшийся дефицит в вибраторах для кассетных установок; затянувшийся вопрос с реконструкцией конвейерных линий, не оснащенных виброуплотняющими устройствами; хранение на одном складе пяти видов заполнителей, в том числе трех видов шебня.
Решение этих и ряда других вопросов будет способствовать дальнейшей экономии цемента на Ростокинском заводе ЖБК.
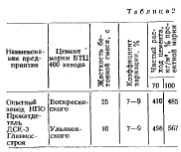
Выводы
В вибропрокатной технологии наиболее эффективным является использование цементов с высокой прочностью после ускоренных высокотемпературных режимов ТВО.
Выбор эффективного цемента в сочетании с оптимальной жесткостью бетонной смесн позволяет значительно сократить его расход. Проектная марка бетона М300 при 70% отпускной прочности в вибропрокатной технологии может быть достигнута при жесткости бетонной смеси 25 с и расхода цемента БТЦ 400 Воскресенского завода 350 кг/м3.
Бетон и железобетон, 1987