Ф. А. ГОФШТЕЙН, канд. техн. наук (Карагандинский Промстройпроект), Стальная фибра из отходов
Эффективность сталефибробетона в значительной степени зависит от вида и методов получения используемых фибр.
В настоящее время известно четыре способа изготовления фибр: из проволоки с резкой и профилированием на специальных станках [1]; из стальной полосы заданной ширины с поперечной резкой специальными фрезами ; из стального слитка путем фрезерования [2]; вытяжкой волокон из расплава [3].
Первые три способа основаны на переработке дефицитной металлургической продукции, стоимость получаемых фибр весьма высока — от 240 до 450 р. При вытяжке фибр из расплава возникают технологические сложности, что затрудняет широкое использование этого метода в промышленном производстве. Таким образом, известные способы получения фнбр не позволяют осуществить широкое использование сталефибробетона в строительстве из-за высокой стоимости и дефицитности материалов, а также из-за технологических трудностей.
Одним из перспективных путей получения стальных фибр является использование отходов — отработанных канатов, некондиционного тонкого стального листа и обрезков, отходов проволоки и т. д. Применение отходов позволяет утилизировать вторичные ресурсы, значительно снижается стоимость исходного материала (30...50 р т) и конечного продукта— фибра (70...130 р/т).
Следует отметить, что в стране имеется достаточное количество отходов, из которых можно получить стальную фибру необходимого качества и относительно невысокой стоимости и обеспечить потребности строительства в стальной фибре. По данным НИИЖБ, в ХН-й пятилетке необходимо получить около 12... 15 тыс. т стальной фибры. Ежегодно в стране сдается около 650 тыс. т отработанных канатов, среднее количество отходов тонколистовых прокатных станов равно 5...6%, при работе только одного стана мощностью 500 тыс. т получается около 25...30 тыс. т отходов.
В Карагандинском Промстройпроекте в течение ряда лет ведется разработка методов и технологического оборудования для получения стальных фибр из отходов. Первоначально совместно с ЦНИИпромзданий и ЛенЗНИИЭП был предложен способ получения фибр из отработанных канатов с использованием термической обработки Канаты предварительно отжигали при температуре 100...1000°С, затем разрезали на отрезки заданной длины. Путем перетирки отрезки расщепляли.
Опытное изготовление фибр по этому методу показало, что при температуре свыше 300С происходит возгорание сердечника и смазки каната, а регулировать процесс отжига практически невозможно. Кроме того, температура внутри каната и на его поверхности существенно различается, поэтому механические характеристики фибр имеют значительный разброс, а их прочность снижается. При термической обработке возникает большое количество газов, отжиг необходимо производить в специальной камере (типа горна) с мощной вытяжной вентиляцией. Кроме того, отожженные канаты перед подачей на резку необходимо очищать от продуктов сгорания, в случае технологическое оборудование засоряется. Все это значительно снижает эффективность предложенного способа.
С учетом указанных недостатков были предложены методы получения фибр из отработанных канатов, исключающие термическую обработку при высоких температурах. Они предусматривают предварительную резку канатов, перетирку прядей с последующей очисткой острым паром с добавлением моющих средств или сухую очистку фибр.
В Карагандинском Промстройпроекте разработана рабочая документация опытно-промышленной установки для получения фибр из отработанных канатов. Изготовленная на одном из заводов Караганды установка в течение года эксплуатируется на заводе жаростойкого бетона треста Казметаллургстрой.
В состав установки (рис. 1) входит вертушка для бухт канатов, подвижная каретка для закрепления конца каната, режущий диск и барабанная дробилка. Бухту отработанного каната устанавливают на вертушки, конец закрепляют в каретку, передвигаемую с помощью пневмоцилиндра. Падающим вращающимся диском осуществляют резку каната. Опускание диска и его возврат в исходное положение выполняются пневмоцилиндром.
Отрезанные на заданную длину пряди каната попадают в четырехвалковую дробилку, где их расщепляют на отдельные фибры. Процесс получения фибр осуществляется в автоматическом режиме. Длина прядей регулируется в зависимости от диаметра проволок каната для получения фибр с отношением l/d= = 100. Из дробилки фибра попадает в дозирующие емкости и на очистку.
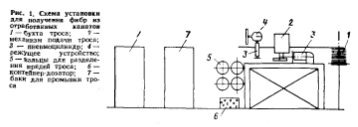
На установке можно осуществлять резку канатов практически любого диаметра. Производительность установки — 250 кг фибры в смену, стоимость 1 т опытной партии фибры по утвержденной расценке— 130 р.
На указанную фибру разработаны ТУ 67-797-86, утвержденные Минтяжстроем СССР. В настоящее время в институте разрабатывается автоматизированная линия по производству фибр из отработанных канатов.
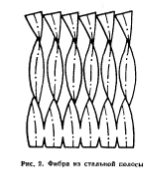
Наряду с достоинствами (высокая прочность, низкая стоимость, наличие сырья) стальная фибра из отработанных канатов имеет и ряд недостатков: технологические сложности при устранении сердечника и смазки, наличие в одной партии фибр разного диаметра, комкуемость их при длительном хранении. По нашему мнению, такую фибру целесообразно производить в пределах одного строительного подразделения (треста, комбината, объединения). Учитывая небольшие размеры подобных установок, их можно разместить на свободных площадях заводов ЖБИ.
Для централизованного изготовления и поставки можно рекомендовать фибру, получаемую из отходов тонколистовых станов. Она представляет собой стальную стружку, изогнутую в продольном направлении по винтовой линии (рис. 2). На поверхности стружки имеются продольные ребра, образованные гранями ее поперечного сечения, ориентированные, в свою очередь, по винтовой линии, описанной вокруг винтовой продольной оси.
Стружки с помощью поперечных перемычек объединены между собой в пакеты. Такая форма обеспечивает хорошую анкеровку фибры в бетонной матрице. Объединение фибр в пакеты препятствует их комкованию при транспортировании и хранении. Разделение пакета на отдельные элементы происходит при их смешивании с бетоном, что улучшает распределение фибр в бетоне и повышает технологичность процесса перемешивания.
Изготовление стальной фибры производится путем последовательно осуществляемых продольной и поперечной резки полосы Образование пере.мычкн происходит при продольной резке за счет выемок в режущих кромках ножен.
Предложенный способ позволяет использовать полосы стали шириной не менее двух ширин стружки (1,5..2,0 мм), то есть практически любые отходы полосовой стали требуемой толщины. что наряду с простотой изготовления обеспечивает низкую стоимость арматуры (до 60 .. 70 р/т). Следует отметить. что такая фибра имеет гарантированные физико-механические и химические свойства, поскольку изготовляется из металла, имеющего стандартны-: показатели.
Линии по производству стальной листовой фибры целесообразно устанавливать ка тонколистовых прокатных станах у агрегатов продольной резки.
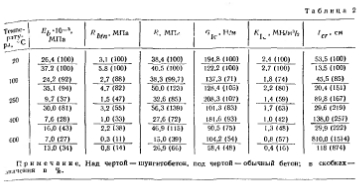
В настоящее время в Карагаидинскс Промстройпроекте ведется разработка рабочей документации опытной линии по производству фибры из отходов тонколистовых станов. Ведутся также поиски по изготовлению фибр из отходе а других видов.
Полученные на основе полных диаграмм деформирования шунгитобетона нормального твердения данные по прочности, энергетическим и силовым параметрам, трещиностойкости, их изменению при воздействии температур 100, 250, 400 и 600°С позволяют запроектировать конструкции необходимой надежности, прогнозировать поведение конструкций из шунгитобетона при высокотемпературном воздействии (пожаре).
Бетон и железобетон, 1987