Э. 3. ЖУКОВСКИЙ, д-р техн. наук, Ю. А. ЧАРУЙСКИЙ, В. Ф. ШАБЛЯ, кандидаты техн. наук, В. Н. ЛУКИН, инж., Монтаж сборной оболочки рынка и ее исследование при раскружаливании
Покрытие Даниловского рынка (Москва) представляет собой сборно-монолитную железобетонную составную оболочку циклического плана пролетом 72 м, опирающуюся по периметру на 14 контрфорсов (рис. 1). Она состоит из 14 складчатых оболочек ромбического плана, между которыми расположены консольные оболочки треугольного плана.
В центре покрытия предусмотрено фонарное отверстие диаметром около 15 м, перекрытое полусферической сетчатой оболочкой; по периметру сооружения расположены контурные арки. Все железобетонные оболочки собирали из сборных унифицированных плитоболочек, включенных в Территориальный каталог ТКД — 3 [1...3].
Кольцевые усилия пространственной системы покрытия воспринимаются в трех уровнях: вверху — фонарным кольцом, в середине — металлической кольцевой распоркой в вершинах консольных оболочек, а внизу — железобетонной подземной затяжкой, соединяющей все контрфорсы по периметру сооружения. Покрытие рынка разработано МНИИТЭПом.
В основу монтажа этого большепролетного покрытия положен принцип укрупнитедьной сборки. На нулевых отметках расположены 6 сборочных стендов, на которых собирали укрупненные секции оболочек трех основных типов (рис. 2). Секции размером 6Х Х12 м складчатого поперечного сечения монтировали из четырех плит. Максимальный вес каждой секции составлял около 16 т. 11осле замоноличивания швов между плитами специальным захватом секции устанавливали в проектное положение. Для стабилизации поперечного сечения служили поперечные затяжки и распорки.
Для установки укрупненных секций в проектном I положении предусмотрена монтажная оснастка, состоящая из трех замкнутых рядоз монтажных стоек, объединенных системой горизонтальных балок и наклонных связей. Оспнстка разработана ВНИПИПроектстальконструкцией.
Наружный кольцевой ряд оснастки включал 28 монтажных стоек, расположенных под опорными элементами оболочек. Средний ряд состоял из 14 стоек, находящихся в вершинах консольных оболочек, где расположена замкнутая металлическая распорка сооружения. Под фонарным кольцом были предусмотрены 14 стоек внутреннего ряда. Все 46 монтажных стоек имели снизу песочницы для осадки после сборки всей конструкции.
После установки укрупненных секций и контроля геометрии их соединяли между собой стыковыми накладками; между плитами укладывали продольную арматуру, затем швы и монолитные участки конструкции замоноличивали бетоном класса В22,5. Расход материалов на 1 м2 покрытия: бетона — 0,152 м3, стали — 48 кг.
Раскружаливание столь сложного пространственного покрытия являлось ответственной операцией, потребовавшей тщательной подготовки. Термин раскружаливание весьма условен, поскольку оболочки собирали не на деревянных кружалах, а на разреженных металлических стойках.
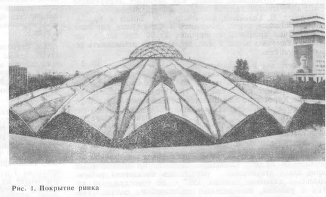
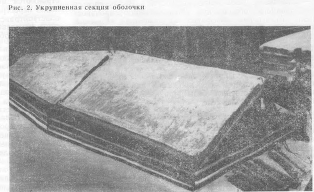
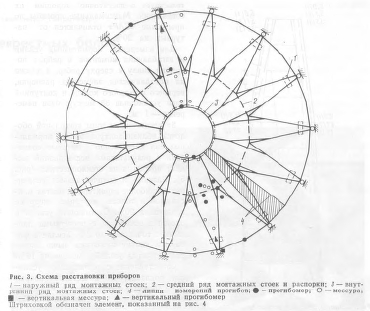
Сущность раскружаливания заключалась в процессе перехода конструкции от монтажной к эксплуатационной стадии освобождением ее от монтажных стоек.
МНИИТЭПом была разработана методика раскружаливания покрытия, предусматривающая определенную очередность работ, продолжительность операций и т. д. Были установлены приборы для измерения прогибов, горизонтальных перемещений и относительных деформаций покрытия, оценки напряженно-деформированного состояния конструкции в этой стадии и проверки расчетных и экспериментальных данных. Производили также визуальный осмотр конструкции с целью фиксации трещинообразования.
В процессе раскружаливания осуществляли поэтапную осадку монтажных стоек с измерением перемещений и деформаций. Для контроля осадки монтажных стоек к верхним листам песочниц приваривали штыри, а на нижние трубы наносили мерные риски. Для извлечения песка из отверстий песочниц изготовили из скрученной металлической полосы штыри в виде шнеков.
Раскружаливание покрытия осуществлял трест «Стальконструкция» под техническим руководством циклами, каждый включал три этапа.
Сначала производили одновременную и плавную осадку на 10 мм монтажных стоек среднего кольцевого ряда. Для этого вскрывали боковые отверстия в корпусах всех песочниц и извлекали песок с контролем осадки но мерным рискам. Через 15 мин снимали отсчеты по всем приборам и производили визуальный осмотр конструкции. На втором этапе осуществляли одновременную п плавную осадку на 5 мм монтажных стоек наружного кольцевого ряда. Цикл завершался одновременной и плавной осадкой па 5 мм монтажных стоек внутреннего ряда, расположенных под фонарным кольцом.
Такая очередность и величина синхронной осадки рядов монтажных стоек были приняты заранее по результатам статических расчетов покрытия в этой стадии, а также в соответствии с эпюрами прогибов конструкции.
После. завершения первого цикла работ, в ходе которого осадка всех монтажных стоек составила 5 .. 10 мм, выполнили второй цикл, аналогичный первому и т. д.
За 6 циклов общая осадка стоек — 70.. 150 мм. Отрыв монтажной оснастки, определенный по стабилизации прогибов конструкции, произошел во время второго и третьего циклов. Поэтапная осадка монтажных стоек после третьего цикла была увеличена до 20 .. 40 мм в каждом цикле.
В конце каждого этапа после снятия отсчетов по приборам и визуального осмотра конструкции обрабатывали полученные данные для определения параметров напряженно-деформированного состояния оболочек. Для этого строили графики прогибов по всем измеряемым точкам и устанавливали усилия в кольцевом распорном кольце покрытия. Только после этого приступали к работам па следующем этапе.
Для контроля за напряженно-деформированным состоянием покрытия было установлено 40 мессур с точностью измерения деформаций и перемещений 0,01 мм, два прогибомера с точностью измерения также 0,01 мм и 12 прогибомеров с точностью измерения вертикальных перемещений 1 мм (рис. 3). Две месеуры фиксировали вертикальные перемещения опорных узлов, расположенных один против другого двух складок вдоль их продольных осей, а два прогибомера служили для измерения горизонтальных перемещений. Показания этих приборов позволили установить, что на первых этапах происходила некоторая подвижка опорной грани складок (до 0,4 мм вдоль оси складки) вследствие неплотностей в шарнирах. Однако в последующем это смещение прекратилось, что свидетельствует о несмещаемости опор в процессе раскружаливания.
Наиболее подробно определяли напряженно-деформированное состояние двух противолежащих складок и примыкающих к ним консольных оболочек.
На трещины, образовавшиеся во время монтажа, были поставлены гипсовые маяки. Визуальным наблюдением установлено, что эти трещины далее не развивались. Новых трещин не появилось.
Максимальный прогиб был отмечен в зоне крепления кольцевой распорки (11,5 мм) (рис. 4). В пересчете па полную нормативную нагрузку (7Н = 0,6 Па) это соответствует соотношению прогиба к длине пролета /даоо, что свидетельствует о высокой жесткости покрытия. Прогиб в центре покрытия составляет 52% максимальных величии.
Сопоставление полученных результатов измерений прогибов при раскружаливании покрытия с прогибами модели этого покрытия из стеклопластика в масштабе 1:30 при нагрузке <7=0,34 Па, соответствующей собственному весу конструкции, показывает их хорошее совпадение. Максимальные прогибы отличались на 14, а прогибы в зоне фонарного кольца всего на 5%. Это подтверждает упругую работу покрытия во время раскружаливания.
Сравнение прогибов покрытия при раскружаливания и результатов расчетов методами конечных элементов но программам, «SAP», и «ФИНИК» свидетельствует о достаточно хорошем их совпадении. Максимальные прогибы по программе «SHP» отличаются от натурных на 20%.
Для измерения нормативных усилий и изгибающих моментов в ребрах покрытия снизу и сверху ребер, а также на металлических элементах распорки, верхнего фонарного кольца и контурной арки установили 38 мессур; база измерения — 1 м.
За исключением зоны консольной оболочки вблизи контура эпюры нормальных сил качественно полностью совпадали с результатами исследований модели покрытия из стеклопластика (рис. 5). Разница в количественных величинах в наиболее характерных местах максимумов и точках перелома эпюр не превышала 20%. Сжимающие усилия в распорке совпадали с расчетными данными с точностью до 2%. Усилие в фонарном кольце оказалось выше экспериментальных усилий в модели на 19%.
Сопоставление с расчетными усилиями показало, что качественно покрытие работало в соответствии с расчетной схемой и результатами расчета. Количественное различие было несколько больше, хотя и здесь сопоставление с результатами нормальных сил в средней зоне покрытия (в зоне крепления распорки) с результатами по программе «5ЛР» выявило различие 2... 27%. Расхождение в этой же зоне с результатами, полученными по программе «ФИНИК», несколько больше.
Расчетные сжимающие усилия в распорке по программе «ФИНИК» оказались меньше натурных всего на 6, а по программе «SAP» — больше натурных на 25%.
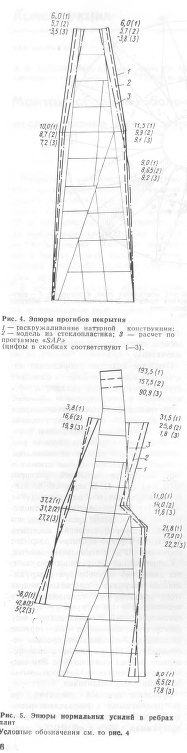
Следует отметить, что напряженно-деформированное состояние натурного покрытия оказалось близким результатам экспериментально-теоретических исследований конструкции в упругой стадии.
Данные исследований указывают на эффективную работу составной оболочки как в меридианальном, так и кольцевом направлениях. Несмотря на сложную геометрическую форму, удалось скомпоновать конструкцию из сборных унифицированных плит с максимальным числом типоразмеров. Работа покрытия в кольцевом направлении обеспечивалась конструктивными сопряжениями составляющих оболочек и в дополнение к ним — кольцевой распоркой.
Наблюдениями в течение 2 мес за деформациями кольцевой распорки установлено, что при постоянной нагрузке во времени усилия практически не увеличиваются, что свидетельствует о стабилизации напряженно-деформираванного состояния конструкции.
Выводы
Успешное раскружаливание пространственного покрытия сложной формы показало высокую эффективность методики совмещения монтажных и научно-исследовательских работ, в ходе которых были достигнуты четкая очередность и синхронность работ.
Полученные данные указывают на достаточную прочность и трещиностойкость конструкции, а также ее высокую жесткость, что свидетельствует о надежности возведенных оболочек рынка.
Бетон и железобетон, 1988 №02