Г. А. ОБЪЕЩЕНКО, С. М. ТРЕМБИЦКИЙ, кандидаты техн. наук (ВНИИжелезобетон), Эффективные тепловые методы интенсификации твердения бетона
Время тепловой обработки сборного железобетона в современном производстве достигает 80 % общей продолжительности производственного цикла.
В последние годы основное внимание на заводах сборного железобетона уделяли повышению эффективности эксплуатации теплоиспользующего оборудования, выполнению комплекса доступных каждому заводу мероприятий по нормализации технологического тепло- потребления, внедрению новых эффективных тепловых установок с повышенной теплозащитой ограждающих конструкций н энергосберегающих технологий с использованием пара, электроэнергии, продуктов сгорания природного газа и различных видов возобновляемых источников энергии.
После проведения энергосберегающей кампании в 1981 —1985 гг. заводское технологическое теплопотребление в промышленности сборного железобетона сократилось на 7...Ю % и стабилизировалось на уровне 1,25—1,40 при нормативных значениях 0,75... 0,84 ГДж/м3. Таким образом, дополнительный резерв экономии технологических энергозатрат составляет 35... 40%.
Применяемые до сих пор на заводах ЖБИ мероприятия и разработки (1...3) направлены на снижение расхода и экономию тепловой энергии и топлива без сокращения производственного цикла изготовления изделий.
В настоящее время 80 % формовочной оснастки и тепловых установок заводов сборного железобетона эксплуатируется с одним оборотом в сутки и только 15 % — имеют полтора оборота. В настоящее время требования к производству резко возросли, поэтому необходимо создать не только малоэнергоемкое, но и более интенсивное производство сборного железобетона с двух- и трехкратной оборачиваемостью теплоиспользующих установок и формовочной оснастки в сутки.
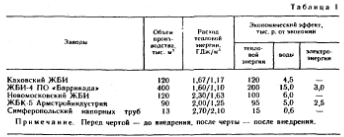
Получение бетона заданных свойств в короткий срок при минимальной фондоемкости производства не может быть обеспечено какой-то одной мерой. На всех этапах технологического процесса, начиная от подготовки исходных материалов и кончая тепловой обработкой, целесообразно использовать весь комплекс технологических приемов и воздействий, приводящих к сокращению общего цикла изготовления изделий и улучшению качества продукции.
Для этой цели применяют разнообразные методы активизации твердения бетона (механические, химические, температурные и электрофизические воздействия). Однако максимальная эффективность воздействия достигается, как правило, в сочетании с тепловой обработкой.
Проанализируем методы теплового ускорения гидратации цемента и структурообразования бетона, технологические приемы и теплотехническое оборудование, обеспечивающие максимальное сокращение общего цикла.
Новые представления о механизме гидратации цемента позволили более точно определить необходимое время активной тепловой обработки.
Повышение температуры цементного теста эффективно ускоряет гидратацию минералов цемента в кинетической области, а при возрастании диффузионного сопротивления гидратных слоев доступ воды в непрогидратнрованную область цементных зерен (агрегатов) становится затруднительным, скорость гидратации падает и происходит смена механизма гидратации на диффузионный. В связи с этим дальнейшее тепловое воздействие становится малоэффективным.
ВНИИжелезобетоиом разработай новый способ тепловой обработки железобетонных изделий с ограниченным тепловым импульсом. Изделия разогревают до расчетной температуры и выдерживают в тепловых установках до достижения переходного периода процесса гидратации. Дальнейшее твердение бетона осуществляется в режиме остывания в тепловых установках или вне их; причем кинетика твердения остается неизменной, как при изотермическом выдерживании.
Режимы тепловой обработки бетона с ограниченным тепловым импульсом апробировались в промышленных условиях по двум направлениям.
Первое — использование энергосберегающих режимов. При этом экономический эффект достигается благодаря не только экономии тепловой энергии, но и сокращению тепловых установок и увеличению оборачиваемости форм. Так, промышленные испытания новой технологии тепловой обработки на Кавказском заводе железобетонных шпал показали, что время пребывания изделий в камерах сокращается на 50 %, металлоемкость парка форм снижается на 20 %. Одновременно с этим расход тепловой энергии сокращается на 30 %
Второе направление предполагало получение максимальной экономии тепловой энергии при существующих режимах работы установок. В этом случае изделия разогревают до температуры, обусловленной активностью при пропаривании, требуемой оборачиваемостью установок в сутки, заданной распалубочной или передаточной прочностью бетона изделий, а также длитедьностью остывания камер с изделиями, т. е. их тепловой инерцией.
Экономия энергии при таких режимах достигается ограничением подачи теплоносителя на стадии разогрева изделий до расчетной температуры, которая в большинстве случаев меньше на 10... 30°П стандартной (80...90°С). Расчетная темература определяется по методике [3].
В качестве примера в табл. 1 приведены технико-экономические показатели предприятий, внедривших эту технологию. Из этих данных следует, что экономия тепловой энергии и питьевой воды, необходимой для подпитки котлов, колеблется от 25 до 40 %. Там, где в результате экономии энергии удалось остановить котлы (ЖБК-5 и ЖБИ-4), снижается и расход электроэнергии на 10...15 % за счет остановки насосов, вентиляторов и дымососов.
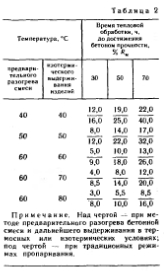
Качественный скачок в интенсификации производства, снижении его фондоемкости, в том числе энерго- и металлоемкости, и в создании прогрессивных компоновочных решений технологии заводов сборного железобетона возможен на основе сочетания методов приготовления теплого бетона и ограниченного теплового импульса.
Методы приготовления теплого бетона направлены на достижение более интенсивного по сравнению с традиционным паропрогревом твердения бетона.
Для максимально возможного ускорения твердения бетона в более ранние сроки советскими учеными в 60...70-е годы был предложен и разработай метод предварительного разогрева смесей. Известно, что время твердения при использовании теплых бетонов в 2...3 раза меньше, чем при традиционных режимах пропаривания.
Однако попытки внедрить новый метод в существующие технологические линии были неудачны. На некоторых предприятиях не получено никаких преимуществ из-за большой скорости охлаждения разогретой смеси во время ее транспортирования к месту формования. Это приводило к тому, что смесь, разогретая до 40...60 0 С, после укладки а форму имела температуру 20 ° С. Внедрение этого метода с разогревом смеси перед укладкой в форму также оказалось малоэффективно из-за незаинтересованности предприятий в увеличении производительности н неподготовленности оборудования технологических линий.
Дальнейшие работы по усовершенствованию действующего и созданию нового оборудования для приготовления и формования теплого бетона в заводских условиях были практически прекращены. Однако при монолитном возведении зданий н сооружений в зимних условиях этот способ стал основным.
В табл. 2 даны усредненные значения циклов тепловой обработки бетона класса В22.5, приготовленного на цементах группы при различных температурных воздействиях и методах тепловой обработки.
По сравнению с традиционными режимами пропаривания метод применения теплого бетона позволяет в 1.8... 2 раза сократить время достижения бетоном распалубочной (50% RK), передаточной, или отпускной (70 % R„) прочности, резко увеличить съем продукции с 1 м2 производственной площади и снизить фондоемкость производства.
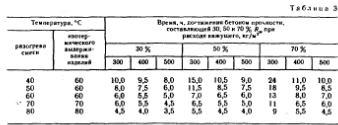
Эффективность применения интенсивных тепловых методов ускоренного твердения бетона повышается при использовании химических добавок. Так, введение суперпластификаторов 40-03, С-З и других позволяет снизить температурный уровень нагрева смеси с 80 до 60°С без изменения общей продолжительности цикла тепловой обработки для равноподвижных смесей.
Предлагаемые методы интенсификации изготовления изделий эффективны и при использовании новых вяжущих, например вяжущего низкой водопотребности ВНВ. Кинетика твердения бетона на ВНВ отличается чрезмерно длительным индукционным периодом, который не позволяет при твердении в нормальных условиях повысить оборачиваемость форм выше 1 оборота в сутки. Поднять этот показатель до 2... 3 оборотов можно с помощью тепловой обработки.
Наиболее интенсивный рост прочности бетона в ранние сроки твердения наблюдается прн ускоренных методах тепловой обработки с использованием теплых бетонных смесей или ускоренного разогрева изделий с малой открытой поверхностью.
В табл. 3 приведено время твердения бетона на ВНВ-50 (цемент Здолбуновский) до заданного уровня прочности в процессе тепловой обработки с применением предварительного разогрева смеси с О.К.=6...8 см.
Сопоставляя данные табл. 3 с аналогичными характеристиками твердения разогретых бетонных смесей - на обычных цементах И группы (см. табл. 2), можно отметить равную эффективность применения теплого бетона, приготовленного на портландцементах и ВНВ при 70...80 ° С. При понижении температуры разогрева смеси до 40 ° С эффективность применения ВНВ возрастает, дополнительно экономит до 30 % топливно-энергетических ресурсов. При этом следует учитывать значительную экономию топлива в цементной промышленности в результате снижения расхода цемента.
Технология тепловой обработки бетона с ограниченным тепловым импульсом отличается тем, что при достижении бетоном прочности, равной 30... 40 % R„. формы с изделиями можно извлекать из тепловой установки и дальнейшее твердение бетона осуществлять в режиме охлаждения.
В связи с этим применение теплых смесей в сочетании с технологией ограниченного теплового импульса позволяет еще более интенсифицировать процесс тепловой обработки и практически отказаться от традиционных установок, что и обусловливает более эффективные компоновочные решения технологического оборудования заводов нового поколения.
Интенсивные методы ускорения твер- дення бетона можно реализовать на различных тепловых установках с использованием известных энергоносителей (пара, электроэнергии, продуктов сгорания природного газа, вторичных энергоресурсов и т. д.).

Высокоэкономичные тепловые режимы с предельно коротким временем активной тепловой обработки бетона основаны на индивидуальном подходе к производству с учетом вида изделий и технологии их изготовления. Технические решения интенсивной малоэнергоемкой тепловой обработки изделий могут иметь различные варианты.
К ним относятся ускоренный прогрев отформованных изделий и последующая их выдержка в режиме изотермы, термоса или остывания. Примером указанного варианта является технология индукционного нагрева железобетонных плит, труб, опор ЛЭП и т. д., позволившая по сравнению с паропрогревом снизить энерго- и металлоемкость производства на 30...50 %. Интенсификация производства при этом выражается почти двухкратным увеличением оборачиваемости форм и съема изделий с единицы производственной площади.
Бетон и железобетон, 1991