Н. А. БОЧАРОВ, В. Н. РОССОВСКИЙ, кандидаты техн. наук (ВНИИжелезобетон); Т. В. КУЗНЕЦОВА, д-р техн. наук, проф., Н. С. НИКОНОВА, В. В. МИТЮШИН, кандидаты техн. наук, О. Н. МАТЮХИНА, инж. (МХТИ), Особенности раздельного приготовления бетонных смесей
При заводском изготовлении железобетонных изделий для увеличения их выпуска и сокращения сроков строительства зданий из монолитного бетона требуются цементы повышенной прочности с интенсивным нарастанием ее в ранние сроки твердения. Применение для этих целей специальных быстро- твердеющих и высокопрочных цементов связано с большими энерго- и топливными затратами. Известно, что потенциальные возможности цемента реализуются не полностью, что приводит к значительным его потерям.
Одним из способов совершенствования использования цемента и интенсификации его твердения является интенсивная гидромеханическая активация, обусловливающая раздельное приготовление бетонной смеси. Степень гидромеханического воздействия определяется линейной скоростью вращения ротора смесителя-активатора и продолжительностью обработки.
Физико-механическне свойства бетонов, приготовленных по традиционной технологни, зависят от способа измельчения цемента, его гранулометрического состава, а также от кристаллической структуры, сформировавшейся в процессе твердения. Чем тоньше измельчен цемент, тем интенсивнее он гидратируется и твердеет. Роль отдельных фракций цемента в формировании прочности цементного камня неоднозначна — фракция 0...5 мкм способствует росту прочности в первые 24 ч твердения; фракция 7...30 мкм определяет рост прочности до 28 сут и качество цемента в целом; фракция 30...60 мкм способствует росту прочности после 28 сут твердения, фракция 60... 120 мкм и более медленно гидратируется в течение длительного времени, уплотняя цементный камень .
Авторы исследовали процессы, происходящие с цементными частицами в условиях интенсивной раздельной технологии приготовления бетонной смеси в сравнении с обычной, и их влияние на физико-механические свойства бетонного камня. Для экспериментов использовали цемент завода «Гигант», содержащий 65 % алита, 15 % белита, 7 % трехкальциевого алюмината и 13 % четырехкальциевого алюмоферрита.
Бетонные смеси готовили по обычной и интенсивной раздельной технологии с расходом цемента 305, песка 750. щебня 1075, воды 220 кг/м3.
При интенсивной раздельной технологии весь цемент и 70 % общего содержания песка обрабатывали в смесителе-активаторе с постоянной скоростью 16 мс прн В/Ц=0,55 в течение 30, 60 и 120 с, а затем активированную цементно-песчаную смесь перемешивали 120 с в смесителе с остатком песка и крупным заполнителем при В/Ц=0,72. По обычной технологии время перемешивания в смесителе — 180 с.
В процессе обработки цементно-песчаного раствора в активаторе отбирали пробы, которые моментально обезвоживали для предотвращения дальнейшей гидратации. Из них выделяли цементные составляющие, в которых определяли фракционный состав частиц на лазерном анализаторе размеров частиц фирмы «Malvern» (Великобритания), принцип действия которого основан на расшифровке дифракционной картины, образующейся в результате рассеяния лазерного излучения на исследуемых микрочастицах. Изучали также фракционный состав цементных составляющих бетонных смесей.
Бетонные образцы, полученные по обычной и интенсивной раздельной технологиям, твердели в условиях пропаривания при температуре 80°С по режиму З+З+б+З ч и в условиях нормального твердения. Испытания на прочность при сжатии проводили через I и 28 сут. Результаты обрабатывали методом пошаговой регрессии иа ЭВМ «МЕРА — КАМАК» с использованием прикладных программ «Векторный калькулятор», разработанных в МХТИ.
Получены уравнения регрессии, связывающие содержание фракций размером >65; 30...65; 5,8...30 и <5,8 мкм цементной составляющей бетонной смеси, полученной по обычной и интенсивной раздельной технологиям, со временем обработки т в смесителе-активаторе.
Характер распределения частиц по фракциям после обработки в активаторе и смесителе в зависимости от времени активации представлен на рис. 1, причем распределение частиц при т=0 соответствует исходному негидратированному цементу и распределению частиц в цементной составляющей бетонной смеси, полученной по обычной технологии.
Следует отметить, что при производстве бетонной смеси как по обычной, так и по интенсивной раздельной технологиям в начале взаимодействия цемента с водой происходит дезагрегация основной массы частиц крупных и средних фракций, а количество самых мелких частиц (<5,8 мкм) практически не меняется. После активатора преобладает фракция 5.8...30 мкм, хотя в исходном цементе основная доля приходится на более крупную фракцию (30... 65 мкм). В процессе активации основные изменения происходят с самой крупной фракцией размером >65 мкм — через 60 с активации ее количество уменьшается практически до 0, но при увеличении времени пребывания материала в активаторе сверх оптимального количество крупных частиц снова возрастает в основном вследствие уменьшения доли фракции 5,8...30 мкм
После обработки материала в бетоносмесителе количество мелких фракций 5,8...30 мкм и <5,8 мкм увеличивается во времени. Содержание самой крупной фракции (>65 мкм) минимально через 80...90 с активации.
Изменения, происходящие с частицами цемента при обработке в активаторе и смесителе согласуются с изменением удельной поверхности 5уд цементной составляющей бетонной смеси, измеренной методом низкотемпературной адсорбции азота. Так после смесителя по обычной технологин увеличилась с 0,29 у исходного негидратированиого цемента до 0,59 м2/г. При интенсивной раздельной технологии после обработки в активаторе в течение 90 с 5уд составляла 0,7, а после смесителя возросла до 0,8 м2/г.
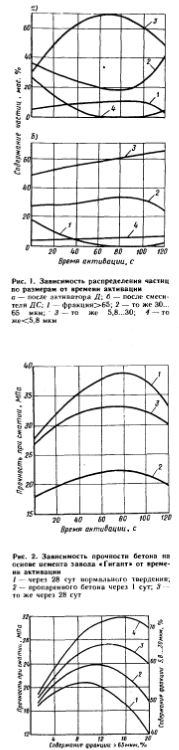
Методом пошаговой регрессии получены уравнения, связывающие прочность бетона после пропаривания через 1 и 28 сут, а также через 28 сут нормального твердения со временем активации т (рис. 2). Все кривые изменения прочности проходят через максимум, соответствующий времени активации 70...90 с. Дальнейшая обработка цементно-песчаного раствора в смесителе-активаторе снижает прочность бетона. Эти результаты согласуются с данными распределения частиц по размерам — рост прочности сопровождается снижением содержания частиц размером >65 мкм вплоть до 0, а происходящее затем снижение прочности связано с повышением доли этих частиц, что вызвано агрегированием мелких частиц при увеличении продолжительности активации.
Для бетонов на основе цемента завода «Гигант» были получены уравнения регрессни, связывающие прочность с распределением частиц цемента по размерам. Для пропаренных бетонов в возрасте I сут
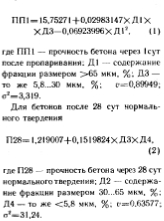
Следует отметить, что для пропаренных бетонов наиболее существенное влияние на прочность оказывают частицы размером 65 мкм и 5,8 ..30 мкм, а для бетонов нормального твердения— чистицы размером 30.. 65 мкм и <5,8 мкм.
На рис. 3 представлены кривые зависимости прочности пропаренного бетона от содержания фракций размером >65 и 5,8...30 мкм. Наибольшая прочность может быть достигнута при содержании 10...20 % частиц размером >65 мкм и 60...70 % фракции 5,8... 30 мкм.
На практике для бетонов нормального твердения на основе цемента завода «Гигант» наиболее близкое к оптимальному распределение частиц наблюдается при получении бетонной смеси по интенсивной раздельной технологии при продолжительности обработки цементно-песчаного раствора в смеси- теле-активаторе 60...90 с.
Для пропаренных бетонов оптимальное содержание 10...20 % фракций размером >65 мкм и 60...70 %, 5,8—30 мкм, обеспечивающее максимальную прочность, при интенсивной раздельной технологин не достигается. По-видимому, в данном случае следовало бы применить цемент более грубого помола. Это объясняется тем, что при ТВО гидратация мелких фракций происходит слишком интенсивно, в результате чего в камне создаются большие внутренние напряжения. Однако и для пропаренных бетонов при интенсивной раздельной технологии достигается прочность, превышающая аналогичный показатель по обычной технологии, на 25...30 %.
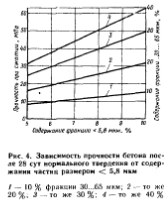
Выводы
Установлено, что в процессе обработки цементно-песчаного раствора в смесителе-активаторе происходит разрушение агломератов, приводящее к значительному увеличению в материале доли мелких фракций и, как следствие, к повышению гидратационной активности цементной составляющей.
Прочность бетонных образцов, полученных при оптимальном режиме интенсивной раздельной технологии, увеличивается на 25...30 %, что дает возможность получать заданную прочность при меньшем расходе цемента.
Бетон и железобетон, 1991