А. С. АРБЕНЬЕВ, д-р техн. наук, проф. (Владимирский политехнический ин-т); Н. П. РОЩУПКИН, инж. (ПМК-242 Ленстройкомитета) Виброэлектробетонирование на стройплощадке
В ПМК-242 Ленстройкомитета ежегодно укладывается около 7 тыс. м3 бетона, транспортируемого на расстояние до 100 км. Зимой для прогрева бетона требуется много электродов, проводов,электроэнергии. С учетом работы автокрана стоимость уложенного бетона достигает 51 р/м3 при сметной стоимости 22 р/м3.
В 1985 г. началось внедрение в производство более эффективной технологии виброэлектробетонирования, разработанного Владимирским политехническим институтом [1] и запатентованного в 12 зарубежных странах. После обработки бетонной смеси в виброэлектрореакторе полностью исключается электропрогрев бетона, а следовательно, электроды н разводящие провода, снижается расход электроэнергии. При этом резко активизируется цементное тесто, позволяющее сократить потребность в цементе, и благодаря последующему естественному выдерживанию бетона значительно улучшаются свойства бетона. Кроме этого снижаются трудозатраты из-за совмещения приема, транспортирования, разогрева и вибрирования смеси в одном агрегате, а также исключения крана при бетонировании фундаментов [2].
По данным технико-экономического расчета, утвержденного Главвладимирстроем, минимальная прибыль с 1 м3 уложенного бетона составляет 5.1 р.. а с одного виброэлектрореактора — 137,7 тыс. р. Однако виброэлектрореакторы, изготовленные СКВ Строймеханизация Минстроя СССР, оказались неработоспособными из-за полного пренебрежения данными экспериментальных исследований.
В связи с этим ПМК-242 обратилась непосредственно к авторам разработки, н в октябре 1989 г. такая установка была изготовлена и испытана за 2 сут из подручных материалов. Представители ЛИСИ отметили ее высокую мобильность, производительность и экономичность при абсолютной безопасности работ.
Изготовленный виброэлектрореактор представляет собой обычную стальную трубу с входным и выходным вырезами, подвешенную на тросах и снабженную двумя периодически работающими вибраторами. Внутрь трубы коаксиально установлен асбестоцементный стержень, на котором смонтированы электроды из кровельной стали, к последним изнутри трубы подключен кабель. Все соединения выполнены без сварки, с прокладкой амортизирующей резины для полного устранения виброшума (см. рисунок). Для загрузки бетона предусмотрен раздельный бункер, для выгрузки — отверстие, расположенное в целях устранения заторов между вибратором и подвеской.
Таким образом, в виброэлектрореакторе соединены в единое целое элементы вибролотка и вибромаятника, электробункера и соленоида, пропарочной камеры и автоклава. В результате использования энергетических воздействий всех видов: потенциально- и вибромеханнческнх, электротепловых и электромагнитных, термохимических и барофазовых — полностью устранены потерн энергии, и коэффициент полезного действия достигал 0,94.
Изготовлено несколько типов виброэлектрореакторов. Первый применяли для подогрева и перемешивания раствора при каменной кладке с целью исключения дефицитного и дорогого поташа. В зимних условиях обработанное пластифицированное цементное тесто до замерзания успевало насытить кирпич водой и связать всю свободную воду, что обеспечивало дальнейший после оттепели набор прочности.
Затем внброэлектрореактор использовали при бетонировании фундаментов.
Для этого его подвешивали к каркасу, передвигаемому на полозьях, и бетон непосредственно из бетоновоза поступал в бункер.
Фундаменты бетонировали с модулем поверхности 6 при температуре наружного воздуха — 10 СС из бетона класса В15 с O.K.=6...8 см, которая после обработки смеси возрастала до 8...10 см. Поток бетона зависел от осадки конуса и угла наклона трубы, но, главным образом, от непрерывности поступления бетона (простои достигали 30%).
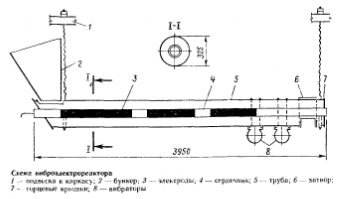
Температура разогрева смеси пропорциональна времени разогрева бетона и силе тока, зависящей от степени заполнения трубы. При перерывах в поступлении бетона сила тока снижалась от 400...450 А до 0 и в среднем составила 200 А. В связи с этим требуемая мощность достигала 300 кВт при мощности 150 кВт, и в среднем расход энергии составлял 40 кВт/м3.
Обработка данных показала, что поток бетона П6 в смену можно определить по простой зависимости от угла наклона грубы р и подвижности смеси
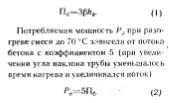
От колебаний силы тока возникал перекос фаз, однако на наружной поверхности трубы из-за электромагнитного экрана полностью отсутствовало напряжение.
Бетой укладывали без вибрирования и немедленно укрывали рубероидом. Температура смеси на выходе и в конструкции в зависимости от увеличения потока соответственно снижалась (см. таблицу). После окончания работ стержень вынимали и трубу очищали банником. Время остывания бетона до 0 °С составило 2...3 сут. прочность бетона до замерзания достигала 50...80 % марочной.

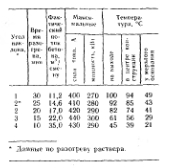
За счет отказа от крановщика и стропальщика, а также круглосуточного дежурства электрика и электромонтеров по монтажу электродов и электропроводов экономия последних составила до 10 кг/м число рабочих сократилось до семи. Общая экономия в зависимости от условий бетонирования составила 5...30 р/к бетона.
Минсевзапстрой РСФСР утвердил временные технические условия по виброэлектробетонированию, а НИИЖБ на базе ПМК-242 в начале 1991 г. наметил провести в Ленинграде Всесоюзное совещание-семннар по виброэлектробетонированию. В настоящее время разработаны рабочие чертежи виброэлектрореактора, которые вместе с техническими условиями можно получить по договору (600026, г. Владимир, ул. Горького, 89, ВПИ НТ1Д).
Бетон и железобетон, 1991