С.Л.НЕРУБЕНКО, В.А.ГВОЗДЕВ, кандидаты техн. наук (26 ЦНИИ МО РФ), О совершенствовании методов испытания бетона на морозостойкость
В [1] поднят весьма актуальный вопрос об испытаниях бетона на морозостойкость и показано, что регламентированные ГОСТ 10060-87 методы обладают рядом недостатков. По нашему мнению, наиболее существенным из них является проведение испытаний не до разрушения образцов, а до заданного, определяемого маркой по морозостойкости, числа циклов. В результате фактическая морозостойкость бетона, как правило, остается неизвестной.
Тот факт, что в конструкции и сооружения укладывается бетон с неопределенной морозостойкостью, является ключевым во всей системе обеспечения долговечности бетона. При таком подходе отсутствует обратная связь с нормами по морозостойкости, так как из практики эксплуатации в этом случае невозможно установить, какой морозостойкостью должен обладать бетон для обеспечения требуемой долговечности конструкций, работающих в тех или иных условиях. Еще одним негативным последствием является невозможность оценки однородности бетона по морозостойкости, которая необходима как при нормировании морозостойкости, так и при прогнозировании развития морозных разрушений и планировании на основании этого сроков и объемов ремонтных работ.
Указанные обстоятельства являются непреодолимым препятствием на пути совершенствования действующих нормативных требований к бетону по морозостойкости. В связи с этим мы полагали бы необходимым пересмотр всей концепции обеспечения морозостойкости бетона, в том числе разработку новых методов ее определения.
Опираясь на свой 20-летний опыт работы над проблемой морозостойкости бетона, авторы видят два принципиальных пути развития методов испытаний: совершенствование существующих методов, регламентируемых ГОСТ 10060-87 и предыдущими его редакциями, и разработка новых, учитывающих специфику работы бетона в конструкциях различного назначения.
Основным требованием к методам определения морозостойкости бетона должно быть доведение образцов до разрушения в процессе их замораживания и оттаивания. Под разрушением в данном случае подразумевается не дезинтеграция образцов в буквальном смысле, а доведение их до “отказа”, т.е. до потери ими критической доли контролируемой характеристики. При этом очевидным требованием при назначении величины критерия морозостойкости является обеспечение достоверности получаемых результатов.
А.М.Подвальный [1] совершенно справедливо критикует действующий ГОСТ 10060-87 за недостоверность получаемых при испытаниях бетона на морозостойкость результатов, что обусловлено несоответствием границы прочностного критерия и однородности прочности бетона. Однако при использовании формул математической статистики автор допустил досадные неточности, что несколько исказило количественную оценку этого несоответствия.
Предположим, имеются две серии образцов бетона из одного замеса, предназначенных для испытания на морозостойкость. Число образцов в каждой серии равно п. При определении средней прочности_бетона получены значения R] и R2 . Средние R] и R2 — нормально распределенные случайные величины с параметрами распределения
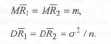
Для оценки вероятности того, что при испытании второй серии значение R2 выйдет за пределы допускаемого стандартом снижения прочности по отношению к R], рассмотрим случайную величину S= R2-R\. На основании свойства линейности нормального распределения случайная величина § также имеет нормальное распределение с параметрами [2]
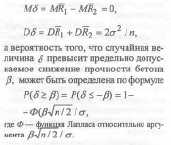
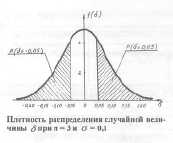
Результаты расчета показывают, что при 5%-ном критерии, установленном ГОСТ 10060-87, любой бетон без испытания на морозостойкость с вероятностью до 30% может быть признан неморозостойким. С другой стороны, с той же вероятностью этот же бетон, в процессе испытаний на морозостойкость снизивший прочность на 10% и более, будет признан морозостойким (см. рисунок). Таким образом, следует признать, что стандартный метод испытаний в редакции 1987 г. не позволяет достоверно дифференцировать бетоны по морозостойкости.
В связи с вышеизложенным авторы считают целесообразным при пересмотре стандарта число образцов в серии для определения прочности в каждый срок испытания назначать равным 3...6 в зависимости от значения среднего внутрисерийного коэффициента вариации, а предельно допускаемое снижение прочности после требуемого числа циклов замораживания и оттаивания принять равным 10%. Это позволило бы оценивать соответствие морозостойкости бетона требуемой марке с доверительной вероятностью 0,9...0,95. Представляется, что некоторое увеличение трудоемкости испытаний не является чрезмерной платой за получение достоверных результатов.
Утверждение А.М.Подвального о недопустимости увеличения прочностного критерия противоречит основному лейтмотиву его статьи и не согласуется с реальной ситуацией: к сожалению, долговечность бетонных и железобетонных конструкций при переходе от 15%-ного критерия (ГОСТ 10060-76) к 5%-ному (ГОСТ 10060-87) не повысилась. Нетрудно убедиться, что увеличение прочностного критерия с 5 до 10% не повлечет за собой сколько-нибудь существенного ослабления требований к морозостойкости бетона. Например, вероятность признания морозостойким бетона с фактической потерей прочности более 20% при предлагаемом подходе и по ГОСТ 10060-87 приблизительно одинакова и составляет 3...4%.
Следует подчеркнуть, что, по нашему мнению, основные (базовые) методы испытаний должны основываться именно на принципе циклического замораживания и оттаивания, как наиболее близко моделирующем условия работы бетона при природных воздействиях. Методы же, основанные на других принципах, например, дилатометрический, структурно-механический, следует отнести к косвенным. Для них, по аналогии с определением прочности, необходима увязка с основным методом, так как по своей сути они не могут учесть в полной мере всех факторов, определяющих реальную морозостойкость такого сложного гетерогенного материала, как бетон. По этой причине маловероятно, что для этих методов могут быть получены универсальные корреляционные зависимости с основными методами; сопоставительные испытания, по-видимому, необходимо проводить в каждом конкретном случае.
Серьезный недостаток прямых методов определения морозостойкости — большая длительность испытаний, достигающая порой 1 ...2 лет. Сокращение сроков испытаний может быть достигнуто за счет ужесточения условий испытаний путем понижения температуры замораживания образцов в каждом цикле до минус 50°С. При этом за основу могут быть приняты уже апробированные методы и коэффициенты перехода от числа циклов к маркам по морозостойкости: для бетона конструкций, работающих в пресной воде, — ускоренный метод ГОСТ 10060-76 с замораживанием на воздухе и оттаиванием в воде; для бетонов дорожных и аэродромных покрытий, а также других конструкций, эксплуатирующихся в присутствии растворов солей,—третий метод ГОСТ 10060-87.
Снижение температуры замораживания до минус 50°С позволит сократить срок испытаний в 5... 10 раз и, например, для бетона марок по морозостойкости F200...F400 при выполнении двух циклов замораживания и оттаивания в сутки довести продолжительность испытаний до 2...5 недель.
Как уже отмечалось, при осуществлении контроля за состоянием бетона в процессе испытаний на морозостойкость по изменению его прочности показатель морозостойкости и однородность бетона по этому показателю остаются неизвестными. В связи с этим было бы целесообразно если не заменить, то по крайней мере дополнить контроль по прочности неразрушающими методами, например, как это предусматривается в стандартах некоторых зарубежных стран, определением динамического модуля упругости или скорости ультразвука. При этом прочность правильнее было бы оценивать после числа циклов, соответствующих марке по морозостойкости и далее — после критического уменьшения значения показателя, определяемого неразрушающим методом, т.е. после числа циклов, определяющих фактическую морозостойкость бетона.
По мере накопления экспериментальных данных можно было бы в конечном счете отказаться от контроля по прочности. В самом деле, процесс морозного разрушения заключается в постепенном образовании тупиковых микротрещин, их накоплении и объединении. Как свидетельствуют результаты исследований [3, 4], скорость ультразвука в некоторой степени является более чувствительным показателем, чем прочность, по отношению к таким структурным изменениям. Контроль за состоянием бетона неразрушающими методами в процессе испытаний позволил бы отказаться от контрольных образцов, что повысило бы достоверность получаемых результатов.
Для отдельных видов железобетонных конструкций, которые эксплуатируются в специфических условиях или к которым предъявляются особые требования, представляется целесообразной разработка специальных методов определения морозостойкости. К таким конструкциям, например, относятся дорожные и аэродромные покрытия, для которых морозные повреждения всегда локальны и начинаются с поверхности. При этом даже незначительные поверхностные разрушения существенно ухудшают показатели ровности и снижают безопасность эксплуатации, что недопустимо.
Для определения стойкости бетона к шелушению 26 ЦНИИ МО РФ в течение 10 лет применяется специальная методика [5], которая заключается в попеременном замораживании на воздухе и оттаивании в растворе соли поверхностного слоя (3...5 мм) образца со стороны испытуемой грани; остальной объем образца при этом постоянно остается замороженным. Степень разрушения бетона в ходе испытаний контролируется по изменению объема образцов, определяемого гидростатическим взвешиванием. Принятые режимы испытаний позволяют оценивать стойкость поверхностного слоя бетона к шелушению за 1...2 недели.
Характер разрушения образцов при испытаниях предлагаемым способом аналогичен шелушению поверхности покрытий дорог и аэродромов.
Авторы данной статьи, излагая свой взгляд на проблему определения морозостойкости бетона, не претендуют на полноту охвата связанных с ней вопросов и не считают все изложенные положения единственно верными. По-видимому, учитывая сложившееся неблагополучное положение с долговечностью бетонных и железобетонных конструкций, необходимо не только продолжить начатую журналом дискуссию по этим вопросам, но и предусмотреть проведение исследований по решению многих из них с привлечением широкого круга заинтересованных организаций.
Бетон и железобетон, 1998 №5