Б.И.БАХТИН, канд.техн наук (МЭИ); И.Б.ЗЕЛЕНОВ, канд.техн. наук, проф., К.И.ЗЕЛЕНОВ, инж., Б.А.УСОВ, канд.техн. наук (МГОУ); А.И.ИВАШОВ, канд.техн. наук (МГТУ им.Баумана), Газодинамическая ударно-волновая технология изготовления бетонов
При изготовлении бетонных и железобетонных изделий в заводских условиях, а также в монолитном строительстве широко применяют динамические воздействия на бетонную смесь с использованием гармонических колебаний или ударно-волновых процессов [1-4]. Практическая реализация таких воздействий чаще всего осуществляется с помощью различных типов электромеханических вибраторов. Как правило, они работают при неизменных (либо слабо изменяемых) амплитудно-частотных характеристиках, не обеспечивающих оптимальных условий формования и уплотнения бетонных смесей.
Предлагаемая [5-8] принципиально новая газодинамическая ударно-волновая технология (ГУВТ), не использовавшаяся ранее в строительной технике, позволяет регулировать динамическое воздействие в заданных пределах на различных этапах и стадиях обработки бетонной смеси. Технология основана на преобразовании тепловой энергии, выделяющейся при быстром сгорании (детонации) порций газовой или аэрозольной топливной смеси в ударно-волновых газодинамических устройствах (УВГУ). Реализация ГУВТ дает возможность, в частности, уплотнения жестких бетонных смесей, что является практически неразрешимой проблемой при применении традиционных технологий.
Этап уплотнения бетонных смесей принято подразделять на три стадии [2,3]. На каждой из этих стадий требования по уровню амплитудно-частотных характеристик динамических воздействий, а также по величине статических нагрузок могут заметно отличаться. Судя по литературным данным, уточнение оптимальных значений указанных параметров продолжается до настоящего времени. Обобщение данных позволяет выделить ряд закономерностей процесса уплотнения бетонных смесей. На всех стадиях процесса необходимо обеспечить условия виброожижения смеси, заключающееся в том, что период колебаний должен быть меньше времени ее релаксации, которое возрастает с увеличением жесткости обрабатываемой среды. )Для подвижных смесей этому условию отвечает минимальная частота вибровоздействия на уровне нескольких герц, для жестких смесей (90... 100 с) частота может возрасти до 40... 50 Гц.
На первой стадии уплотнения (переукладка составляющих смеси, вытеснение газовых пузырей) внешнюю статическую нагрузку применять не рекомендуется. Оптимальная частота гармонической динамической нагрузки составляет для подвижной бетонной смеси 15...25 Гц, что связывают с резонансной частотой крупных частиц заполнителя. Опыт показывает, что переход от гармонических колебаний к импульсным (ударным) и от моночастотных к поличастотным повышает эффективность уплотнения смеси. Это может быть объяснено выходом на резонансные частоты мелких частиц заполнителя и пузырьков воздуха (сотни герц и более), что сопоставимо с собственными частотатми импульсов (fc) ударных вибраторов. Амплитуда динамического давления должна быть выше некоторого минимального уровня (предположительно порядка 0,1 МПа).
На второй стадии уплотнения (сближение составляющих) требуемый эффект достигается главным образом путем увеличения амплитуды динамического давления (примерно до 0,3 МПа), а также статического давления (примерно до 0,1 МПа) за счет дополнительной внешней нагрузки. Для удаления мелких пузырьков воздуха желательно также дальнейшее повышение частоты динамического воздействия. Высказывались даже предположения (не проверенные на практике) о перспективности перехода к ультразвуковому частотному диапазону. Однако верхняя допустимая граница частотного диапазона вряд ли может выходить за пределы 1...5 кГц из-за сильного затухания высокочастотных волн в бетонной смеси.
На третьей стадии уплотнения (компребсия смеси) динамическую и статическую составляющие амплитуды давления целесообразно довести примерно до 1 МПа (дальнейшее увеличение заметного эффекта практически не дает). Требования по частоте динамического воздействия должны ограничиваться, по-видимому, из условия обеспечения виброожижения смеси.
С учетом изложенных закономерностей можно представить возможный характер изменения по времени параметров воздействий при виброуплотнении, например, жестких бетонных смесей (рис.1) с использованием гипотетического ударно-волнового устройства, имеющего регулируемый уровень собственной частоты (fc) и амплитуды давления (Р), а также частоты следования импульсов, или частоты циклов (f4). Величина (f4)mjn соответствует нижнему пределу частотного диапазона, при котором обеспечивается условие виброожижения смеси. Статическое напряжение ас в начальный момент времени определяется собственным давлением в слое бетонной смеси (на графике принято условное значение --0,02 МПа). Возрастание напряжения со временем создается с помощью внешней нагрузки.
Ни одна из существующих технологий не в состоянии обеспечить необходимое регулируемое изменение режимов обработки бетонной смеси, как показано на рис.1. Большинство устройств работает при неизменных, фиксированных амплитудно-частотных характеристиках и предназначено для выполнения определенных операций с конкретными изделиями. Виброустройства с синусоидальной формой волны обычно функционируют н а одной из дискретных частот в типичном диапазоне 50...100 Гци не генерируют волн требуемого высококачественного уровня (сотни Гц — единицы кГц). Импульсные (ударные) устройства имеют собственную частоту импульса порядка 300 ..500 Гц, которую практически невозможно изменять.
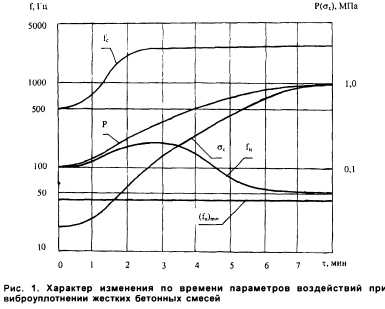
Частота следования импульсов также обычно неизменна. Известны способы формирования в бетонной смеси поличастотного спектра волн путем использования группы локальнодействующих генераторов с относительным смещением фазы волн. Кинематическая сложность таких систем служит препятствием для их широкого использования, несмотря на положительные результаты, полученные в экспериментах. Повышение качества уплотнения смеси наблюдается также при применении виброустройств с так называемыми угловыми колебаниями, однако регулируемое изменение их характеристик в широком диапазоне представляет собой невыполнимую задачу.
Проблемы, связанные с виброуплотнением бетонной смеси, возрастают при выполнении этих операций на строительной площадке, так как устройства должны быть передвижными и при этом иметь возможность подключения к источнику энергоснабжения. Таким образом, качественный скачок в технологии создания бетонных и железобетонных изделий возможен лишь при разработке принципиально новых конструкций, предназначенных для обработки бетонных смесей.
Аналитические и расчетно-экспериментальные проработки, проводившиеся авторами данной статьи на протяжении нескольких лет, позволяют предполагать, что рассматриваемые задачи могут быть успешно решены с помощью газодинамической ударно-волновой технологии.
В основе ГУВТ лежит воздействие от ударно-волновых газодинамических устройств с возможностью регламентированного рассеяния волновой энергии в материале и создании в материалах и средах знакопеременных напряжений сжатия- растяжения в импульсном режиме с различными амплитудно-частотными характеристиками.
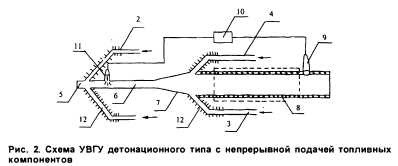
В качестве примера на рис.2 показана схема одного из возможных вариантов установки детонационного типа, работающего с непрерывной подачей газовых компонентов топлива в камеру сгорания.
Это устройство работает на газообразном топливе с частотой циклов до 100 Гц. Горючее и окислитель подаются по коллекторам 1-4, проходящим через холодильники 12 в форкамеру 5, переходник 6, конус 7 и в камеру сгорания 8. После заполнения их горючей смесью датчик 9 с помощью блока синхронизации 10 подает сигнал на поджиг горючей смеси в форкамере 5, осуществляемой свечой поджига
Горючая смесь воспламеняется, дефлаграцинный режим горения переходит в детонационный с возникновением скачка давления, превышающего давление газов в коллекторах, что приводит к прерыванию подачи топливных компонентов. После истечения продуктов сгорания из камеры давление в ней и в коллекторах падает, и процесс повторяется.
Характер изменения по времени давления в волне детонации показан на рис.З.
Величина Рф для газовых смесей лежит в пределах примерно 1...5 МПа. Химические реакции заканчиваются за время т.,, составляющее несколько микросекунд. За это время давление падает в два раза (точка Чепмена-Жуге): Рчж=Рф/2. Если расширения продуктов детонации не происходит, то через время t2, равное примерно 3...5 мс, давление падает до некоторого остаточного (среднего) уровня, составляющего половину давления в точке Чемпена-Жуге: Pcp=P42
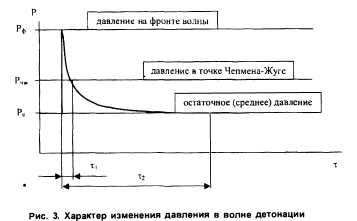
В случае столкновения детонационной волны с жесткой поверхностью в обратную сторону начнет распространяться отраженная волна, давление в которой (Р0т) возрастает по сравнению с давлением (Рчж) в падающей волне примерно в 2,5 раза.
При выходе детонационной волны на свободную границу с воздухом по воздуху пойдет ударная волна, а по продуктам детонации в противоположном направлении со скоростью звука будет двигаться волна разряжения. Ударная волна, скорость которой при перепаде давлений на ее фронте, равном 10, составляет примерно 10ОО м/с, на некотором расстоянии от взрывной зоны перейдет в упругую (акустическую) волну. Давление в этой зоне падает по мере расширения продуктов детонации вплоть до уровня ниже давления невозмущенной окружающей среды. В таблице представлены параметры волны детонации для некоторых газовых смесей.

Таким образом, при детонации газовых смесей возможно появление коротких (микросекундных) импульсов давления с максимальной амплитудой примерно 5 МПа, однако их энергия будет составлять лишь малую часть тепловой энергии продуктов детонации. Основная часть энергии продуктов детонации может быть реализована в волнах давления с амплитудой в пределах около 1 МПа.
Частотные характеристики ударно-волновых газодинамических устройств зависят от их конструктивных особенностей, состава топливной смеси, ее единичного объема. Потенциальные возможности УВГУ позволяют обеспечить любую частоту и амплитуду давления из указанного выше диапазона идеального технологического цикла уплотнения жестких бетонных смесей и их дополнительной обработки. Высокочастотная составляющая импульса (на уровне 1...5 кГц и более) достигается путем прямого удара детонационной волны по твердой поверхности, либо за счет преобразования кинетической энергии струи в акустическую энергию с помощью, например, резонаторов Гартмана. В последнем случае открывается возможность модулирования колебаний (наложение высококачественных пульсаций на основную кривую импульса давления), недоступная для механических виброустройств. Минимальная частота следования импульсов (частота циклов) может составлять доли герц, а расчетная максимальная—достигать уровня 200...250 Гц (при малых объемах камеры сгорания).
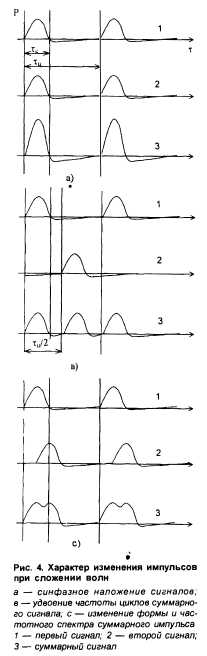
Гораздо более сложной задачей является изменение режимов воздействия в требуемых пределах при уплотнении смеси. Как следует из представленных выше материалов, для смесей средней жесткости частота циклов должна изменяться примерно от 50 до 200 Гц, собственная частота от 500 Гц до 2,5 кГц, амплитуда давления — от 0,1 МПа до 1 МПа.
Указанная выше задача существенно упрощается, если УВГУ выполнять в виде группы взрывных камер с возможностью регулируемого управления их работой. Переход от одной камеры к группе многократно увеличивает вариации выходных характеристик УВГУ. Как известно, при синхронизации связанных колебательных систем, имеющих одинаковые или кратные частоты, возможно деление или умножение, изменение амплитуды и формы суммарного сигнала.
Не касаясь пока технической стороны синхронизации колебательных систем, рассмотрим в качестве иллюстрации некоторые возможные результаты сложения сигналов двух одинаковых импульсных систем (рис.4). При синфазном наложении сигналов (рис.4,а) амплитуда импульса удваивается, а характерные периоды импульса (тс) и цикла (тц) остаются неизменными, а следовательно, не изменяются собственная частота (fc) и частота цикла (f4) суммарного сигнала.
Смещение по времени одного сигнала относительно другого на половину периода цикла (рис.4,в) приводит к удвоению частоты циклов суммарного сигнала. При смещении сигналов в пределах периода импульса изменяются форма и частотный спектр суммарного импульса (рис.4,с) поджига смеси, подобно тому, как это выполняется с помощью системы зажигания в двигателях внутреннего сгорания. Не представляет сложности также изменение в несколько раз частоты циклов в каждой отдельной камере. Варьируя степень заполнения объема камеры топливной смесью, можно в некоторых пределах независимо изменять частоту циклов и среднюю мощность выделения энергии в ней.
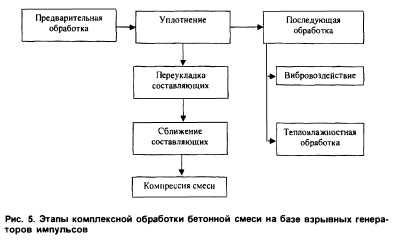
Сложное волновое поле с широким поличастотным спектром может быть создано в объеме бетонной смеси при работе генератора импульсов с группой взрывных камер, разнесенных по поверхности изделия. При этом создается множество комбинаций их совместной работы с одновременным или последовательным инициированием детонации топлива в камерах (во втором случае возникает "блуждающий” источник колебаний), с разделением всех камер на синхронно действующие подгруппы.
УВГУ может быть использовано также на этапах обработки бетонной смеси до ее уплотнения и после. Режимы вибровоздействия на этих этапах существенно проще, чем при уплотнении смеси. Не исключен вариант применения одного и того же генератора импульсов на всех этапах обработки смеси. Кроме того, образующиеся при работе взрывных камер продукты сгорания имеют высокую температуру и содержат пары воды. Их целесообразно использовать для дополнительной тепловлажностной обработки смеси после уплотнения, что может быть особенно важным при монолитном строительстве в холодное время года. Автономность УВГУ дает неоспоримые преимущества технологиям на их основе (по сравнению с традиционными технологиями) в условиях проведения работ непосредственно на строительной площадке или на полигоне.
Таким образом, на базе УВГУ может быть создана комплексная, более совершенная газодинамическая ударно-волновая технология обработки бетонных смесей (в частности жестких) на всех ее этапах (рис.5) как в условиях заводского изготовления изделий, так и на строительной площадке.
В соответствии с предварительными расчетными оценками, внедрение ГУВТ в строительную индустрию может дать существенный технический и экономический эффект. Так, например, только за счет обработки с помощью ГУВТ бетонных смесей повышенной жесткости можно обеспечить снижение расхода цемента на 10...30%, увеличение прочности бетона на 30...70% или уменьшение расхода бетона при создании изделий и конструкций на 25... 50%.
Более подробные сведения можно получить по тел. (095) 219-7070 (Зеленое Иван Борисович).
Бетон и железобетон, 2002 №2