А.В.ПАХОМОВ, инж. (АООТ ,МПЖБ); В.И.БОНДАРЕНКО, канд. техн. наук Е.А.ЧЕРНЫГОВ, инж. (НИИЖБ), Технология арматурных работ при изготовлении блоков обделки автодорожного тоннеля
Для изготовления блоков обделки тоннеля “Лефортово” правительство Москвы приобрело в Германии (фирма Херемкнехт) оборудование фирмы “Ceresola” и ввело его в эксплуатацию в АООТ Моспромжелезобетон” (МПЖБ). Вместе с ним была закуплена проектная и технологическая документация на производство арматуры, арматурных элементов, пространственных арматурных каркасов и железобетонных блоков обделки тоннеля.
По технологическому регламенту фирмы все арматурные элементы пространственных каркасов изготавливают из бунтовой арматуры диаметрами 6... 12 мм класса BSt 500S [1], а при сборке каркасов соединения арматурных элементов осуществляют электросваркой при помощи сварочной проволоки в среде смеси защитных газов (80%Аг + 20% С02).
Поскольку на Российском рынке черного металлопроката бунтовая арматура такого класса прочности и названных диаметров практически отсутствует, было принято решение организовать производство аналогичного класса арматуры (А500С) в АООТ “МПЖБ методом холодной деформации горячекатаной заготовки (катанки).
Так как холоднодеформированная арматура класса А500С является относительно новым видом, в отечественной нормативной документации отсутствуют рекомендации по ее сварке, тем более в среде смеси аргона и углекислого газа. Учитывая это обстоятельство, необходимо было отработать режимы сварки этого вида арматуры и определить их влияние на прочность крестообразных соединений при испытании на срез и ослабление и нахлесточных соединений при испытании на растяжение. Кроме этого, при организации производства арматурных каркасов, согласно проектной документации ОАО “Метрогипротранс”, требовалось обеспечить изготовление линейных и изогнутых арматурных элементов, а также сборку плоских и пространственных каркасов в пределах допускаемых отклонений, которые корреспондируются с размерами опалубок и определяют заданный защитный слой бетона.
На протяжении всего технологического цикла изготовления арматурных каркасов повышенное внимание уделяется контролю качества как самих материалов, так и производства работ. При этом контроль линейных размеров арматурных элементов и каркасов, а также количество и расположение сварных соединений арматуры осуществляет отдел технического контроля, а контроль качества материалов, арматуры и сварных соединений - заводская лаборатория АООТ “МПЖБ.
Для изготовления холоднодеформированной арматуры периодического профиля АООТ “МПЖБ приобрело в Германии четыре прокатных стана с различными усилиями на тянущих барабанах 0 3-6 (KED- 1600), 06-10 (KED-4000) и 010-16 (КН В-5000).
Все станы оснащены разматывателями, петлеуловителями, окалиноломателями, устройствами для нанесения смазки, двумя шестивалковыми неприводными клетями, тянущими барабанами и механизмами намотки арматуры на катушки.
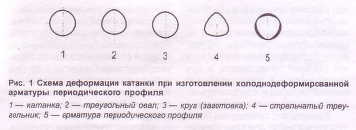
В процессе изготовления арматуры катанка снимается витками с консоли разматывателя, проходит через петлеуловитель, предназначенный для мгновенной остановки стана при наличии в катанке петли или узла, окалиноломатель, где за счет многократного перегиба вокруг роликов освобождается от рыхлой окалины, и поступает в устройство для нанесения на поверхность сухой порошкообразной смазки.
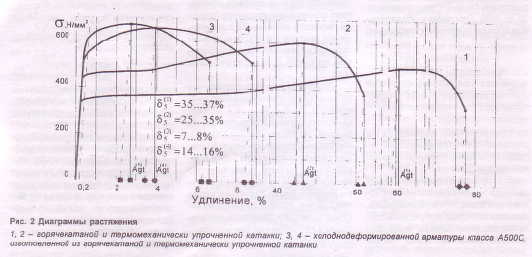
При калибровке катанки за счет объемного обжатия в четырех трехроликовых волоках происходит уплотнение структуры с одновременным повышением прочностных и снижением пластических свойств металла [2], степень изменения которых зависит от химического состава стали, механических свойств катанки и суммарной деформации металла при прокатке.
Для получения арматуры класса А500С, т.е. со значениями условного предела текучести стали более 500 Н/мм2 и при этом с нормируемой [3] пластичностью(§5>14%) исследовали влияние перечисленных факторов на механические свойства арматуры периодического профиля. В результате проведенных работ было установлено, что содержание углерода в стали должно быть в пределах 0,16... 0,22 %, марганца - 0,8... 1,6%, кремния-0,05...0,15%, фосфора и серы - < 0,05% при значении углеродного эквивалента (Сэкв) в пределах 0,3...0,5. При названном химсоставе предел текучести катанки должен быть не менее 450 Н/мм2, относительное удлинение 55> 25% и сужение не менее 60%. Такими свойствами обладает термомеханически упрочненная катанка из стали марки ЗГпс, производство которой осваивают металлургические комбинаты России [4]. На Белорецком металлургическом комбинате освоен выпуск такой катанки диаметрами лишь до 10 мм, что недостаточно для изготовления арматуры номинальными диаметрами 10 и 12 мм, составляющей более 90% по весу от всей арматуры блоков обделки тоннеля.
При изготовлении арматуры класса А500С из такой катанки нет необходимости преднамеренно повышать ее прочностные свойства за счет холодной деформации, так как при нанесении периодического профиля дополнительная деформация составляет около 15%, что достаточно для значения предела текучести более 500 Н/мм2. При такой суммарной деформации катанки ее пластические свойства снижаются менее чем на 10%, что позволяет получить арматуру с пластическими свойствами на уровне требований Евронорм [5] и СТО АСЧМ 7-93 (65>14% Agt>2,5%).
Ввиду отсутствия термомеханически упрочненной катанки требуемых размеров при освоении производства арматуры указанного класса прочности использовали горячекатаную заготовку из стали Зпс с механическими свойствами по ГОСТ 30136 [6].
Минимальную степень суммарного обжатия горячекатаной катанки при изготовлении арматуры устанавливали исходя из обеспечения:
- гарантированного значения условного предела текучести {и0 2>500 И/ММ2);
- регламентированных размеров параметров периодического профиля (fr);
- вытяжки в размере 29%, заложенной в конструкции сдвоенного барабана за счет разности диаметров нижнего и верхнего блоков.
В зависимости от прочностных свойств исходной катанки и ее размеров для получения необходимых прочностных свойств арматуры варьировали степенью деформации от 30 до 40%. При этом в обязательном порядке выполняли требования по обеспечению нормируемых значений критерия анкеровки “fr” (табл. 1), а также учитывали технологическую вытяжку.
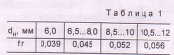
При протяжке арматуры с помощью сдвоенного барабана необходимо довольно точно рассчитывать диаметр заготовки, получаемой после прохождения катанки через первую шестивалковую кпеть, так как при увеличении диаметра заготовки относительно расчетного происходит проскальзывание витков на нижней ступени барабана, что приводит к преждевременному износу его рабочей поверхности, а при уменьшении - к дополнительной вытяжке металла и, следовательно, к уменьшению его пластичности.
В результате проведения перечисленных работ для всех освоенных размеров арматуры были определены необходимые значения прочностных свойств и размеров горячекатаной заготовки из стали марки Зпс по ГОСТ 380 (табл. 2), и разработаны технические условия ТУ 14-1-5393-2000Прокат холодно- деформированный периодического профиля для армирования железобетонных конструкций.
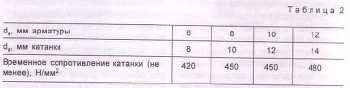
Параллельно с освоением производства холоднодеформированной арматуры класса А500С совершенствовали методику определения ее качественных характеристик.
Для определения прочностных свойств арматуры приобрели разрывную машину марки Zwick Z250 с усилием 25 т. Эта машина в автоматическом режиме выдает диаграмму растяжения образца, определяет значения его условного предела текучести, временного сопротивления, модуля упругости и относительных удлинений при максимальной нагрузке и при разрушении (рис. 2).
Для определения относительных удлинений на различных базах измерения (S5, 510, 6100, 5р) образцы арматуры перед испытанием на разрыв, согласно ГОСТ 12004 (7], необходимо размечать через 10 мм. Для разметки арматуры завод разработал установку, позволяющую наносить риски на образцы арматуры диаметрами от 3 до 40 мм через 10±0,05 мм. Установка успешно эксплуатируется в заводской лаборатории и НИИЖБе уже более года.
Глубину вмятин определяли приспособлением с индикатором часового типа с ценой деления 0,01 мм, оснащенным специальной пяткой. При креплении приспособления на гладкий стержень показания индикатора устанавливают на 0,00. При установке на стержень периодического профиля он показывает максимальную высоту выступа в том месте, где он установлен.
Шаг вмятин измеряли линейкой, а ширину выступов на вершине и расстояние между рядами рифления -лупой Польди {ЛИ-3-10).
Относительную поверхность ребер (критерий анкеровки) “fr” Евронормы рекомендуют определять по формуле
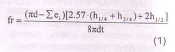
Для расчета “fr” по этой формуле необходимо измерять высоту ребер в четвертях их длины, что не представляется возможным при замерах вручную на стержнях относительно малых диаметров. Учитывая это обстоятельство, мы упростили приведенную формулу, заменив значения “h1/4 и h3/4” на - 2“.
В результате величину “fr” можно определять по формуле с измерением лишь максимальной высоты выступов и суммарного расстояния между концами поперечных ребер.
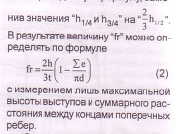
Значения параметров периодического профиля, удовлетворяющие требованиям табл. 1 при расчете “fr по (2), приведены в технологическом регламенте на “Производство и контроль качества проката холоднодеформированного периодического профиля”, разработанного АООТ МПЖБ” совместно с НИИЖБом.
Согласно техническим условиям, приемка несертифицированного проката и катанки производится по характеристическим величинам, а сертифицированного — по гарантированным минимальным значениям. Результаты всех испытаний заносят в специальные ведомости, обрабатывают статистическими методами и представляют главному инженеру для корректировки в случае необходимости технологического процесса.
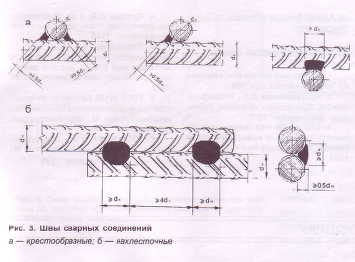
Работы по изготовлению пространственных арматурных каркасов блоков обделки тоннеля состоят из трех основных этапов:
- изготовление арматурных элементов;
- сборка и сварка плоских арматурных элементов (хомутов, сеток и т.д.);
- сборка и сварка пространственных арматурных каркасов
Изготовление отдельных арматурных элементов, предназначенных для сборки плоских и пространственных арматурных каркасов блоков обделки тоннеля, осуществляют на автоматической линии австрийской фирмы “EVG”, где бунтовая арматура по специально заданной программе проходит через правильные устройства, гибочные механизмы и поступает в ножницы для резки.
Правильное устройство за счет знакопеременного изгиба выправляет арматуру, смотанную в бунты или намотанную на шпули, до такой степени, при которой кривизна прутков после правки не превышает 0,6%. ¦
Гибочный механизм обеспечивает загиб выправленной арматуры на любой угол вокруг оправок диаметром, равным от 1 до 5 диаметрам арматуры, и с любым заданным радиусом.
Форма, длина и количество арматурных элементов задаются программой, которую набирают на пульте управления.
Из готовых арматурных элементов на кондукторах собирают и сваривают плоские и объемные элементы. Места контактов и пересечений арматуры должны быть сварены.
Дуговую сварку нахлестанных и крестообразных (без дополнительных технологических элементов) соединений в смеси защитных газов рекомендуем производить при расходе газа 10... 15 л/мин сварочной омедненной проволокой марки Св.08А диаметром 1,2 мм. При этом скорость подачи проволоки должна составлять 8...12 м/мин, а напряжение на дуге находиться в пределах 34...36 В. Размеры швов для крестообразных соединений должны соответствовать приведенным на рис. 3.
Исследования прочности выполненных при помощи контактноточечной сварки крестообразных соединений арматуры класса А500С на срез и ослабление показали, что этот способ сварки можно применять взамен и наряду со сваркой в среде защитных газов.
При контактно-точечной сварке крестообразных соединений арматуры технологические условия должны назначаться в соответствии с требованиями РТМ 393-94 (как для арматуры класса A-IIIB), а их прочность на срез и ослабление должна быть не менее указанной в технических условиях ТУ 5865-00111653082-2002 Каркасы сварные из арматуры класса А500С блоков обделки тоннеля Лефортово, разработанных АООТ МПЖБ совместно с НИИЖБом.
Сборку всех элементов каркаса осуществляют по кондукторам, шаблонам и нивелировочным рейкам и контролируют как в процессе изготовления, так и выборочно на готовых изделиях.
Для определения прочности сварных крестообразных соединений на срез была разработана специальная подвеска к разрывной машине, обеспечивающая опирание поперечного стержня по всей длине и препятствующая его проворачиванию во время испытания. При этом свободный конец нагружаемого стержня поддерживается регулировочным винтом и не может отклоняться от вертикального положения. Апробация этой подвески в течение двух лет показала ее надежность и удобство в работе.
Таким образом, в результате проведения комплекса научно-исследовательских и технологических работ по освоению производства пространственных арматурных каркасов для блоков обделки тоннеля “Лефортово” были освоены:
• технология изготовления холоднодеформированной арматуры периодического профиля класса А500С диаметрами 6... 12 мм из горячекатаной и термомеханически упрочненной заготовки (катанки) •технология и режимы сварки холоднодеформированной арматуры класса А500С как в среде защитных газов, так и при помощи контактно-точечной сварки
• заготовка арматурных элементов и сборка их в пространственные каркасы с соблюдением предельных отклонений линейных и угловых размеров, заложенных в проектной и нормативной документации
• контроль качества поступающей катанки, холоднодеформированной арматуры периодического профиля класса А500С и прочности сварных соединений.
В процессе освоения производства разработаны:
• ТУ 14-1 -5393-2000 “Прокат холоднодеформированный периодического профиля для армирования железобетонных конструкций
• ТУ 5865-001-11653082-2002 Каркасы сварные из арматуры класса А500С блоков обделки тоннеля “Лефортово.
Бетон и железобетон, 2002 №4