С.ГОБЕРИС, И.ПУНДЕНЕ, доктора техн. наук (Институт термоизоляции, Вильнюс, Литва), Жаростойкий керамзитобетон повышенной прочности
Традиционный жаростойкий керамзитобетон (25-40% портландцемента или глиноземистого цемента в составе бетона) широко применяется в конструкциях тепловых агрегатов. Его плотность после сушки в зависимости от насыпной плотности керамзита колеблется в пределах 800-1500 кг/м3, а прочность после обжига при 800°С колеблется в пределах 2-8 МПа [1]. Невысокая прочность после обжига обусловлена разностью деформаций, возникающих при усадке в цементном камне и расширении заполнителя во время нагрева [2]. Известно о значительном повышении прочностных характеристик жаростойких бетонов путем применения микрокомпонентов и пластификаторов [3-5] наряду с уменьшением содержания цемента. Бетоны, в составе которых количество цемента колеблется от 9 до 15% (или, руководствуясь классификацией по количеству СаО в составе, - СаО>2,5%), называются среднецементными. По сравнению с традиционными, среднецементные жаростойкие бетоны характеризуются лучшими реологическими и механическими характеристиками.
В настоящем исследовании показаны возможности повышения прочностных характеристик жаростойкого керамзитобетона при значительно меньшем содержании цемента в его составе.
В работе использовали цемент "Gorkal-40”, микрокремнезем, керамзит, дисперсный шамот и пластификатор. В таком цементе содержание А1203 не менее 40%, FeO+Fe203 - 10,8%. Основные минералогические фазы СаО А1203, ферритная фаза, 12Ca0-7AI203, 2Ca0 AI203 Si02.
Насыпная плотность - 1160 кг/м3, удельная поверхность - 3080 см2/г, огнеупорность не менее 1280°С.
Микрокремнезем изготовлен в Польше. Основные характеристики: Si02 не менее 88%, Fe203 - не более 1,5%, К20 - не более 2%, Na20 - не более 0,6%. Насыпная плотность 330 кг/м3, удельная поверхность- 15-104 см2/г.
Применяли керамзит Палемонского завода (Литва), двух фракций. 0-5 и 5-10 мм. Насыпные плотности соответственно 720 и 640 кг/м3. Водопоглощение фракции 5-10 мм - 14,7%.
Дисперсный шамот приготовлен из лома шамота и просеян через сито с отверстием 0,14 мм. Насыпная плотность 1000 кг/м3, удельная поверхность - 4000 см2/г.
Пластификатор - безводный триполифосфат натрия Na5P3O10.
Для определения влияния микрокремнезема на свойства керамзитобетона заформовано 4 состава, в которых количество микрокремнезема менялось от 0 до 5% (табли- ца).
По данным таблицы видно, что водопотребность, необходимая для получения удобоукладываемой массы, зависит от количества микрокремнезема. Это можно объяснить механизмом взаимодействия частиц микрокремнезема и цемента. Чем плотнее последние покрываются ультрадисперсными частицами микрокремнезема (<1 мкм), тем больше свободной воды остается в массе бетона и его подвижность больше. Количество микрокремнезема, превышающее 5%, не уменьшает водопотребности бетонной смеси и после термообработки вызывает нежелательные усадочные явления в керамзитобетоне.
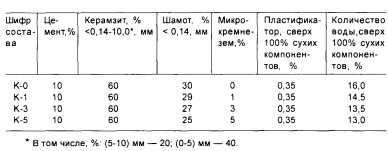
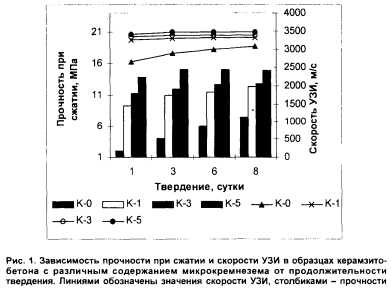
Исследовано влияние количества микрокремнезема и продолжительности твердения на прочность образцов керамзитобетона. Образцы размером 70x70x70 мм были испытаны на прочность при сжатии после 1, 3, 6 и 8 сут твердения в нормальных условиях, одновременно измерена скорость ультразвукового импульса (УЗИ) в образцах.
Как показали результаты исследований (рис.1), прочность при сжатии зависит не одинаково от сроков твердения и количества микрокремнезема. Наименьшая прочность при сжатии получена для состава К-0 без добавки микрокремнезема, хотя прочность его росла практически равномерно в течение 8 сут твердения. При добавке микрокремнезема выявлена тенденция: чем больше содержание микрокремнезема в бетоне, тем выше его прочность при сжатии. Прочность образцов керамзитобетона составов К-1 и К-3 росла до 6 сут, а прочность образцов состава К-5 уже после 1 сут твердения выше, чем у остальных составов, и после 3 сут твердения не изменялась: достигнута максимальная прочность. Следовательно, при добавке микрокремнезема процесс твердения керамзитобетона заканчивается раньше.
Как показали проведенные рентгенографические исследования, в гидратированном связующем керамзитобетона без микрокремнезема основным продуктом гидратации является САН10, причем аморфная фаза неидентифицирована. В связующих керамзитобетона с добавкой микрокремнезема САН10 идентифицировано намного меньше (в 3-4 раза) и большое количество аморфной фазы. В ряде публикаций [6-8] акцентируется, что в период твердения в аморфной фазе связующего с микрокремнеземом протекают реакции, продуктами которых являются субмикрокристаллические гидроалюмосиликаты кальция, обладающие высокой прочностью. Учитывая, что в связующем керамзитобетона К-5 количество аморфной фазы наибольшее, а САН10 наименьшее, по сравнению с другими составами, можно предположить, что в нем образуется больше гидроалюмосиликатов кальция, и этим объяснима его высокая прочность.
Результаты измерения скорости УЗИ в керамзитобетоне (рис. 1) коррелируют с результатами определения прочности. Значение скорости УЗИ в образцах состава К-0 после суточного твердения минимально, но увеличивается в процессе твердения. В керамзитобетонах с добавкой микрокремнезема сохраняется отмеченная выше закономерность - быстрее формируется структура бетона.
Увеличение количества микрокремнезема до 5% увеличивает плотность керамзитобетона после твердения, сушки и обжига, так как структура его уплотняется. Плотность керамзитобетонов после сушки в зависимости от количества микрокремнезема колеблется в пределах 1310-1420 кг/м3, а после обжига при 1000°С от 1280 до 1360 кг/м3. Наибольшее снижение плотности керамзитобетонов наблюдается после сушки (от 6,5 до 10,5% массы образца) из-за удаления слабо связанной влаги в структуре.
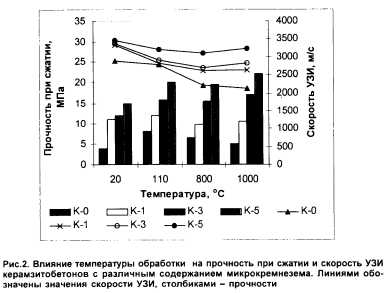
Прочность керамзитобетонов после сушки возрастает (рис.2), поскольку гелевая структура цементного камня из-за выделяющейся влаги уплотняется. После обжига при температурах 800°С и 1000°С прочность керамзитобетонов с микрокремнеземом практически не меняется. Образцы керамзитобетона без микрокремнезема после обжига обладают заметно меньшей прочностью по сравнению с прочностью после сушки.
Ультразвуковые исследования образцов керамзитобетона позволяют объяснить особенности изменений его прочности после термообработки.
Известно, что скорость УЗИ характеризует происходящие в структуре бетона деструктивные процессы, а также влияние температуры на изменения в структуре бетона. Установлено, что после сушки скорость УЗИ в образцах всех керамзитобетонов снижается (рис.2). Химически несвязанная вода, удаляясь из бетона (главным образом из зерен керамзита), вызывает образование воздушных пор, не пропускающих ультразвук. Известно, что в воде скорость УЗИ составляет 1430 м/с [9].
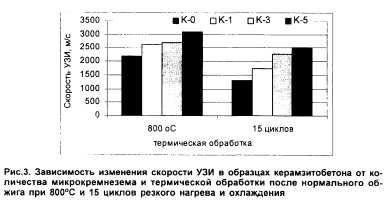
Обжиг при температуре 800°С оказывает деструктивное воздействие из-за образования микротрещин в цементном камне керамзитобетонов, в результате чего скорость УЗИ снижается. В керамзитобетоне К-0 при удалении гидратной влаги получено наибольшее снижение скорости УЗИ по сравнению с другими образцами, что можно объяснить малым количеством аморфной фазы в его структуре. После обжига при температуре 1000°С скорость УЗИ во всех керамзитобетонах за исключением К-0 имеет тенденцию к увеличению, что согласуется с прочностными данными и объясняется спеканием аморфных структур.
Для исследований термостойкости керамзитобетона были использованы высушенные образцы-кубы всех составов размером 7x7x7 см. Притермоциклировании кубы нагревали, помещая их в разогретую до температуры 800°С печь, и охлаждали струей воздуха. Для оценки деструкции керамзитобетонов были замерены скорости УЗИ в образцах после нормального обжига при температуре 800°С (скорость нагрева 2,5°С/мин) и после 15 термоциклов. Сравнение скоростей УЗИ в образцах (рис. 3)показало, что в керамзитобетонах К-5 и К-3 после 15 циклов скорость УЗИ снизилась по сравнению со скоростью УЗИ после нормального обжига при 800°С.
Этим доказывается то, что процессам деструкции более подвержены керамзитобетоны с меньшим количеством микрокремнезема и без него, т.е. микрокремнезем в указанных пределах его содержания в составе способствует увеличению термостойкости керамзитобетона.
Выводы
1. Добавка микрокремнезема до 5% в состав керамзитобетона снижает водопотребность бетонной смеси с 16 до 1 3%. Прочность при сжатии керамзитобетона с 5%-ной добавкой микрокремнезема является максимальной и достигается после первых суток твердения вследствие образования гидроалюмосиликатов кальция.
2. После сушки при 110°С и обжига до 1000°С прочность при сжатии и скорость УЗИ в образцах керамзитобетона зависит от количества микрокремнезема (0-5%) в составе. Добавка микрокремнезема в 2-3 раза увеличила прочность керамзитобетона (до 20 МПа) после термообработки. Среднецементный керамзитобетон может быть применен в качестве конструктивного при сооружении тепловых агрегатов.
3. Исследования скорости УЗИ в образцах керамзитобетона после 15 циклов нагрева и охлаждения -показали, что процессам деструкции менее подвержен керамзитбетон с наличием микрокремнезема в его составе.
Бетон и железобетон, 2002 №6