А.В.ПАХОМОВ, инж. (ОАО «Моспромжелезобетон», Уникальные сборные железобетонные конструкции с новой эффективной арматурой
До последнего времени предприятия сборного железобетона работали, а многие продолжают работать и в настоящее время, на оборудовании и по технологии конца 50-х годов с соответствующими проектами, допусками на размеры изделий, требованиями к бетону и уровню качества арматуры.
Рассматриваемая работа является началом нового этапа развития производства сборного железобетона в России, включающего переход на принципиально новые виды основных материалов: арматуры и бетона, применение высокопроизводительного современного оборудования, технологий и проектов уникальных железобетонных элементов, к которым предъявляются жесткие требования по допускам на размеры, качеству поверхности и долговечности [1, 2,3].
Эти изделия, материалы, технические и нормативные требования соответствуют нормам европейских и международных стандартов и обеспечивают конкурентоспособность сборных железобетонных элементов как с монолитным железобетоном, так и с металлическими конструкциями [1]. В данной работе обсуждаются основные результаты освоения массового промышленного производства уникальных сборных железобетонных элементов из высокопрочного бетона и арматурной стали класса А500С (В500С).
Целью перехода на арматуру класса А500С было:
Обеспечение высокой надежности и исключение хрупких разрушений собственно арматуры и готовых железобетонных изделий;
Улучшение условий и повышение производительности труда на арматурных работах;
Экономия 10-20 % арматурной стали за счет более высоких предела текучести и расчетных сопротивлений арматурной стали класса А500С.
Первые работы по освоению применения стержневой термомеханически упрочненной арматуры ОАО «Моспромжелезобетон» начал совместно с НИИЖБом в 1997-1998 гг. Были проведены испытания опытных партий арматуры и железобетонных конструкций, армированных ею. Промышленное использование ее началось в 1999 г., и уже в 2002 г. применили 1056,23 т стержневой арматуры класса А500С диаметрами 8.. .40 мм производства Белорусского, Молдавского, АО «Северсталь», Запсибкомбината и Магнитогорского металлургического комбината, а также 8766,36 т холодно-деформированной арматуры собственного производства диаметром 5...12 мм.
Установлено, что арматурная сталь класса А500С (В500С) по механическим свойствам и химическому составу отвечает требованиям стандарта СТО АСЧМ 7-93 [3]. Фактические значения предела текучести стт изменялись от 504 Н/мм2 до 796 Н/мм2, временного сопротивления ав от 611 Н/мм2 до 894 Н/мм2 и относительное удлинение 65 от 15 до 29% включительно.
Установленная изменчивость механических свойств стали определяется ее поставками от многих различных металлургических заводов и не выходит за пределы, допускаемые СТО АСЧМ 7-93. Статистические данные о механических свойствах арматурной стали класса А500С за 1999-2004 гг. приведены в табл. 1.
Анализ изменения механических свойств стали класса А500С всех поставщиков и холоднодеформированной стали собственного производства показывает некоторое снижение среднего предела текучести арматурной стали с 600...650 Н/мм2 у арматуры диаметром 5... 10 мм до 550.. .635 Н/мм2 у стержней диаметром 28.. .40 мм.
Основным видом соединения арматурной стали класса А500С (В500С) в каркасы является контактная точечная сварка. Прочность таких сварных соединений регламентируется для этой арматуры нормами ТСН 102-00 и ТУ 14-1-5393- 2000 и должна быть не менее 550 Н/мм2 при испытании образцов на растяжение, т.е. на ослабление рабочего стержня от приварки поперечного и 450 Н/мм2 на срез поперечного стержня при контролируемой прочности на срез.
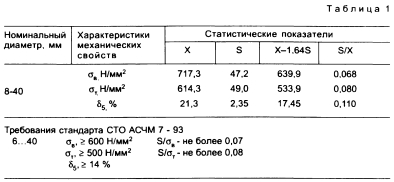
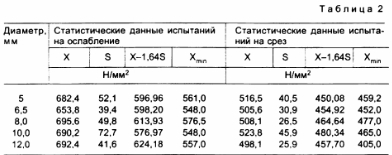
Прочность сварных крестообразных соединений стали класса А500С, собственного производства ОАО «МПЖБ» по результатам испытаний более 1500 образцов хо- лоднодеформированной арматуры приведена в табл. 2.
Контрольные испытания сварных крестообразных соединений холоднодеформированной арматуры класса АбООС/) собственного производства (см. табл.2) показали, что их прочность как по фактическим минимальным значениям Xmjn, так и по расчетным значениям Х-1,64S во всех случаях отвечает нормам ТСН 102-00 [4,5,6].
Для производства основных типов конструкций, тяжелых колонн и элементов системы «Куб» использовали в основном термомеханически упрочненную арматуру класса А500С диаметром 12-40 мм, а для изготовления тюбингов (блоков обделки) тоннелей — холоднодеформированную арматуру класса В500С или АбООСзд) диаметром 6- 12 мм, предусмотренную исходным проектом.
18 сентября 2001 г. распоряжением №80РП Правительство Москвы поручило «Моспромжелезобетону» ежемесячно выпускать по 500 тюбингов для строительства Лефортовского тоннеля. Для этого была осуществлена реконструкция цеха и организовано производство арматурных каркасов и арматуры класса A500C)(B500C). Общий объем перерабатываемой арматуры уже в 2002 г. составил 9000 т.
В результате удалось создать и обеспечить впервые в отечественной практике широкое применение принципиально новых технологий арматурных работ с новой для Рос- сии арматурой класса А500С (В500С), а также освоить промышленное производство уникальных сборных железобетонных элементов, таких как тюбинги (блоки отделки) Лефортовского тоннеля, колонны под нагрузку 1200 т, элементы системы «Куб», балки, плиты и т.п. и обеспечить снижение расхода стали и повышение производительности труда на единицу продукции в среднем на 16% (см. рис. 1 и 2).
Блоки обделки (тюбинги) Лефортовского и Серебряноборских тоннелей представляют собой железобетонные сегменты криволинейного очертания и являются основными частями ограждающей конструкции —сборной обделки кругового сечения диаметром 14,2 м. Она предназначена обеспечить сохранность необходимого для эксплуатации тоннелей подземного пространства и защитить его от воздействия окружающего грунта, грунтовых вод и т.д.
Блоки выпускают из тяжелого бетона класса по прочности на сжатие В45, марки по морозостойкости F300 и водонепроницаемости W12. Фактическая прочность бетона — 600...800 кг/см2. Точность их изготовления характеризуется очень жесткими допусками на отклонение геометрических размеров от проектных: угловые отклонения от 0,01 до 0,04 градуса, линейные — от 0,6 до 3 мм. Производство этих изделий позволило обеспечить значительный экономический эффект за счет уникальных высокопроизводительных технологий изготовления арматурных каркасов и собственно изделий, а также повсеместного применения арматуры класса А500С.
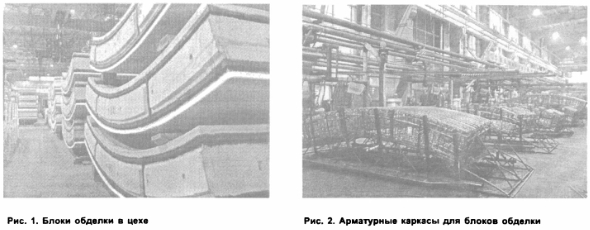
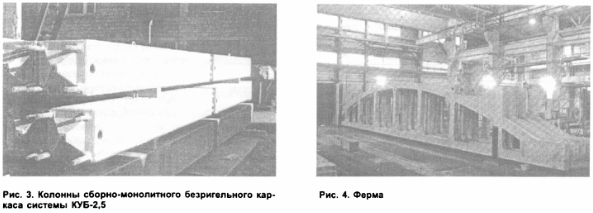
Тяжелые колонны унифицированного каркаса (рис. 3) сечением 400x400 мм изготавливаются из бетона марки М600 и арматуры класса А500С диаметром 25.. .40 мм. За счет применения высокопрочных бетона и арматуры колонны обеспечивают расчетную нагрузку до 1200 т при экономии 20% арматурной стали по сравнению с ранее изготовляемыми из арматуры класса А400.
Технология производства арматурных каркасов колонн высотой до четырех этажей предусматривает стыковку арматурных стержней А500С длиной до 12,5 м с одновременным снятием грата. Сборка объемного каркаса колонн производится в специальном кондукторе, обеспечивающем проектное положение всех элементов конструкции.
Колонны унифицированного каркаса, как и многоэтажные колонны системы КУБ-2,5, изготавливают по двум технологиям: агрегатно-поточной с тепловлажностной обработкой в пропарочных камерах ямного типа и стендовой - в многоместных формах с паровой рубашкой. Установка каркасов и сборка форм по обеим технологиям - аналогична. Изделия формуют на современных виброплощадках с применением высококачественных бетонных смесей. Панели перекрытий с П-образными выпусками под замоноличивание системы КУБ-2,5 армируются плоскими сетками с переменным шагом, в соответствии со схемой нагрузки конструкции, и изготавливают на современных многоточечных сварочных машинах с числовым программным управлением. По этой технологии изготавливают и арматурные сетки из стали А500С для плит аэродромного и дорожного покрытий ПАГ-14 и ПАГ-18.
Широкое применение арматура класса А500С с большим экономическим эффектом нашла и в производстве других уникальных конструкций железобетонных изделий, таких как фермы пролетом 18 и 24 м (рис. 4); стропильные балки пролетом 18 м и др.
Заключение
Впервые после многолетнего застоя осуществлена коренная модернизация производства сборных железобетонных конструкций и изделий.
ОАО «Моспромжелезобетон» совместно с НИИЖБом, ЦНИИСом и другими организациями сделал новый шаг в повышении качества и конкурентной способности сборного железобетона за счет:
• Новых технологий производства и нового более производительного оборудования на всех этапах изготовления сборных железобетонных конструкций (патенты РФ № 2052917 и № 2127229), заявка на патент № 2003119127/03(020730);
• Полного перехода на новую универсальную свариваемую арматуру класса А500С (В500) (патенты РФ № 2166805 и № 32175359), что обеспечивает наряду с коренным повышением качества и безопасности арматурных работ среднее снижение расхода стали на 1 м3 железобетона на 16%, или на 6355 т за рассматриваемый период с 1997 по 2004 г.; новых технологий приготовления и составов бетона (патенты РФ № 2052917 и № 2127229 и заявка № 2003119126/03 (020729), необходимых для обеспечения жестких требований к бетонам уникальных сборных железобетонных элементов и обеспечивших впервые в отечественной практике получение высокопрочных бетонов марок 600- 1000, морозостойкостью F300 и водонепроницаемостью W12-20 при существенном сокращении расхода цемента на 40000 г. с 1997 по 2004 г.;
• Новых уникальных проектов сборных железобетонных конструкций, таких как блоки обделки транспортных тоннелей диаметром 14,2 м, колонны под нагрузку 1200 т, фермы пролетом 18 и 24 м и других изделий, в том числе массовых для дорожного и жилищно-гражданского строительства.
Уникальные железобетонные элементы, изготовленные из высокопрочного бетона и новой арматуры класса А500С, были применены при строительстве Лефортовского и Серебряноборского тоннелей, а также многих других транспортных и гражданских сооружений и жилых зданий в Москве.
Бетон и железобетон, 2005 №5