А.Ф.ШАШИН, инж., Методика расчета анкеров типа “обжатая спираль”
В производстве преднапряженного железобетона в качестве технологической анкеровки при натяжении арматурных стержней используют концевые временные анкеры различного типа. Применение термически упрочненной высокопрочной арматуры классов AIV, AT-V, AT-VI и AT-VII, обеспечивающей повышение напряжений в бетоне, требует использования анкеров высокой несущей способности. Используемая на многих заводах горячая высадка концевых анкеров вызывает разупрочнение этой стали. Этот негативный фактор вынуждает снижать напряжение в арматуре и, следовательно, увеличивает её расход. Высокая материалоемкость в условиях рыночного хозяйствования повышает затратность производства и уменьшает конкурентоспособность выпускаемой продукции.
В настоящее время наряду с “высаженной головкой” для анкеровки высокопрочной арматуры промышленно используются также два типа холоднообжатых анкеров повышенной несущей способности по ТУ 21-33-31-88 [1]. Это - анкер типа “обжатая обойма” для стержней диаметром 10-22 мм и типа “обжатая спираль” для стержней диаметром 10-18 мм.
При равенстве несущей способности этих анкеров “обжатая обойма в изготовлении в несколько раз дороже обжатой спирали”. Этот тип анкеров требует наличия дорогостоящего прессового оборудования для штамповки заготовок- обойм, быстроизнашивающихся штампов и дополнительного расхода листовой стали, идущей в отход. Анкер типа “обжатая спираль” прост и безотходен в изготовлении. Навивка заготовок (спиральных втулок из горячекатаной проволоки) осуществляется, как правило, на станке-автомате. Для опрессовки обоих типов анкеров на стержнях используется в основном пневматическое и гидравлическое оборудование.
За длительный период с момента введения в действие ТУ 21- 33-31-88 до сего дня накоплен значительный опыт использования технологии спиральной анкеровки для арматурной стали диаметром 10-18 мм. Благодаря опыту, накопленному заводами, и исследованиям, проведенным автором, область применения “обжатой спирали” расширена вплоть до арматуры диаметром 25 мм. За это время была проведена модернизация станка-автомата для навивки спиральных втулок и отработана технология изготовления обжимных губок-матриц для обжима анкеров на стержнях диаметром 10-25 мм.
Однако выполненные за это время усовершенствования технологии спиральной анкеровки практически не освещены в технической литературе и не нашли отражения в нормативно-технической документации. Поэтому представляется целесообразным ознакомить читателей с расширением области применения спиральных анкеров и предложить методику их расчета.
Для получения анкера высокой несущей способности применяют заготовку - спиральную втулку с косым срезом проволоки торцевых витков. Проведенные проверки выявили зависимость угла среза торцевых витков спиральной втулки от соотношения диаметров обжимаемой проволоки и стержневой арматуры
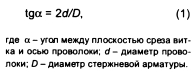
Этой зависимости подчиняются все фактически и теоретически возможные варианты сочетания диаметров проволоки втулок и ар- матуры [2].
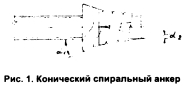
На рис. 1 показана спиральная втулка с косым срезом торца. Такая втулка, одетая на стержень, в обжимных губках опрессовочного устройства получает форму усеченного конуса (рис. 2) или усеченной шестигранной пирамиды (шестигранника) с коническим уширением у опорного торца. Коническое уширение служит для получения потребной опорной площади торца и сокращения числа необжатых или слабо обжатых витков при переходе к обжатым рабочим виткам анкера. Оптимальный угол наклона образующей конического уширения а1 (см. рис. 2) определился в результате исследований и находится в пределах 19-22° в зависимости от диаметров проволоки и стержня [3]. При таком угле наклона возникающее от вертикальной силы обжатия N осевое усилие, определяемое как N tga1, формирует опорный виток в одной плоскости за счет пластической деформации проволоки спирали. Косой срез проволоки торцевого витка заполняет металлом просвет в месте перехода проволоки во второй виток. В усеченном конусе и шестиграннике угол наклона образующей основных рабочих витков а2 колеблется в пределах 3-8° в зависимости от их количества. Этого угла достаточно для пластической деформации и уплотнения рабочих витков проволоки между собой. Это утверждение неоднократно проверялось на продольных шлифах анкеров, срезанных по срединной части и протравленных соляной кислотой. Сформированный таким образом анкер работает как монолит и характеризуется следующими показателями:
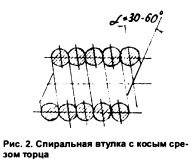
1. Опорный торец лежит в одной плоскости, перпендикулярной оси стержня, и полностью заполнен металлом по всей длине окружности.
2. Погрешность расстояния между обжатыми анкерами на стержне - не более 1 мм при допустимой величине 2 мм и зависит только от точности установки обжимных устройств.
3. Отклонения Р проектного напряжения a = a0±P укладываются в установленные проектные нормативы или имеют разброс напряжения меньше проектного. Так, например, отклонения Р для изделий длиной до 6,5 м (плиты аэродромного и дорожного покрытия ПАГ-14 и ПАГ-18) находятся в пределах ±550 кг/см2 при проектной величине ±800 кг/см2.
Для спирального анкера определяющим фактором потери несущей способности является его срез по внутренней поверхности, образованной диаметром стержня по рифам. Для упрощения расчета принимаем срез по номинальному диаметру стержня О. С этим допущением и проводится расчет анкера на срез (“одёргивание со стержня).
Несущая способность анкера определяется по формуле
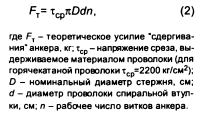
Для обеспечения надежности работы анкера расчет следует вести исходя из допускаемой несущей способности анкера. Выражение (2) примет вид
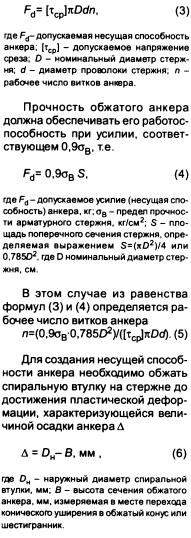
Осадка А имеет существенное влияние на величину несущей способности анкера. В результате исследований определилась зона существования осадки А (зона устойчивых результатов), при которой несущая способность анкера колеблется в пределах усилий, соответствующих 0,9ав-ов арматуры. Эта зона устойчивых результатов для стержней диаметром 10-25 мм существует в пределах 5-7 мм. При А<5 мм происходит преждевременное “одёргивание” анкера со стержня, а при Д>7 мм наблюдаются случаи, когда анкер не срезается, а раскалывается по плоскости разъема обжимных губок.
В производственных условиях осадка анкера А нестабильна и зависит от следующих причин:
- степени изношенности гнезда обжимных губок;
- поля допуска на диаметр арматуры;
- величины усилия пресса и ДР
Поэтому величину осадки Д следует систематически контролировать в процессе изготовления анкеров. С целью повышения степени надежности работы напрягаемых стержней в изделии при нестабильной величине осадки Д представляется необходимым при расчетах увеличить усилие «одёргивания» до величины, соответствующей ав арматуры. При этом величина расчетных рабочих витков анкера увеличится незначительно, а выражение (5) примет вид
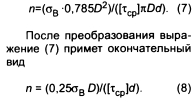
Для определения полного числа витков анкера к расчетному числу рабочих требуется добавить еще один опорный виток, так как он обжат незначительно и лишь облегает стержень, обеспечивая необходимую опорную площадь. Окончательное число витков принимается исходя из технологических возможностей станка-автомата близким к расчетному. При этом надо учесть также тот факт, что в коническом анкере благодаря конической форме гнезда в губках при обжатии спиральной втулки происходит дополнительное закручивание спирали вокруг стержня на 0,25-0,4 витка.
Выражение (8) справедливо при следующих условиях:
1. Используются витые анкеры с коническим уширением у опорного торца, обжатые на конус или шестигранную пирамиду.
2. Диаметры стержневой термически упрочненной арматуры - 10-22 мм для классов прочности AT-IV; AT-V; AVI и AVII. Диаметр арматуры 25 мм следует использовать только для классов А-Ill и A-IV.
3. Для всего диапазона диаметров арматуры применяется гладкая горячекатаная арматурная проволока класса А-I диаметром 6-10 мм с проверкой на смятие опорного торца анкера в упорах формы. Кроме того, для стержней диаметром 10-18 мм классов AIV и AV также может быть использована проволока марки БСтО диаметром 6,5 мм (обычная вязальная проволока).
4. Осадка А должна находиться в пределах зоны устойчивых результатов, т.е. Д = 5-7 мм.
5. Допускаемое напряжение на срез [тср] по результатам исследований принято равным 1500 кг/см2. Для выявления оптимальной величины допускаемого напряжения на срез [тср] проводились многочисленные испытания образцов, при которых находилось минимальное число рабочих витков анкера, обеспечивавших обрыв образца по основному металлу. После чего из формулы (8) определялось [тср]

Эксперименты проводились с образцами арматуры диаметром 10-22 мм классов от A-IV до AT-VII при осадке Д=5-7 мм. Арматура диаметром 25 мм испытывалась только для классов А-Шв и A-IV с анкерами из проволоки диаметром 8 и 10 мм. Расчетные значения [тср] во всех случаях колебались в пределах 1400-1600 кг/см2. Логично предположить, что расчетные значения [Тср] для арматуры диаметром 25 мм классов AT-V, AVI и AT-VII при той же осадке D также будут находиться в указанных пределах. Учитывав сложное напряженное состояние витого анкера, пластически спрессованного на стержне в радиальном и осевом направлениях, принята усредненная величина [тср], равная 1500 кг/ см2.
Для навивки спиральных втулок была проведена модернизация станка-автомата типа МШ-1000, который был использован на заводах КЖИ-100 (г. Сергиев Посад), ЖБИ-18 (Москва) и на других заводах страны. Модернизированный станок имеет набор сменных тяговых роликов, которые позволяют навивать втулки из проволоки диаметром 6-10 мм с минимальными затратами на переналадку. Числа витков спиральных втулок зависят от количества установленных ножей в тяговых роликах. Форма ножа позволяет отрезать втулку с косым срезом проволоки торца.
Для изготовления гнезда анкера в обжимных матрицах (губках) следует использовать комплект из двух нестандартных фрез, предназначенных для выборки конического уширения и основного конуса.
Чертежи модернизированного станка-автомата, обжимных губок для стержней диаметром 10-25 мм и технологической оснастки включены в техдокументацию на разработанную технологию спиральной анкеровки.
Предлагаемая методика расчета позволяет рассчитывать и применять на заводах ЖБИ спиральные анкеры для стержневой высокопрочной арматуры диаметром 10 - 25 мм с использованием электротермического и механического натяжения.
Бетон и железобетон, 2006 №5