А.Г.ЮРЬЕВ, д-р техн. наук, Р.В.ЛЕСОВИК, Л.А.ПАНЧЕНКО, кандидаты техн. наук (БГТУ им. В. Г. Шухова), Дисперсно армированный мелкозернистый бетон с использованием техногенного песка
Мировая практика строительства определила фибробетон как один из перспективных строительных материалов XXI века [1].
Исследование дисперсно армированных цементных композиций позволяет выпускать облегченные строительные конструкции с повышенной прочностью. Помимо экономических соображений, выбор волокна обусловливается тем, какими свойствами должна обладать композиция для удовлетворения заданным требованиям. Изучение возможности замены стекловолокном других волокон в бетоне показало, что получаемый прочный и относительно легкий композит с высокой вязкостью разрушения представляется весьма перспективным.
Увеличение удельной и суммарной поверхностей заполнителя, а следовательно, физико-химической и химической активности частиц достигается посредством добавления мелкозернистого компонента (например, песка) с возможным понижением содержания крупнозернистых фракций. В пределе получают мелкозернистый бетон, когда в качестве заполнителя используют только песок.
Производственная практика показала, что армирование бетона стекловолокном, обладающим высокой химической устойчивостью к щелочной среде, стало возможным благодаря направленной выработке волокон из стекол специальных составов [2, 3]. Использованное в экспериментах цементостойкое волокно выпускается в виде ровинга РЦР-15-190-2520-9. Цифры обозначают: диаметр элементарного волокна в мкм — 15; линейная плотность комплексной нити — 190; линейная плотность ровинга — 500 Н; предел прочности при растяжении — 1600 МПа; предельная деформация при растяжении — 2,2%; модуль упругости — 72 ГПа; модуль сдвига — 29,1 ГПа.
На территории КМА для производства мелкозернистого бетона наибольший интерес представляет отсев дробления на щебень попутно добываемых горных пород (кварцитопесчаников), а также отходы мокрой магнитной сепарации железистых кварцитов. Первые представляют собой почти мономинеральную породу тонкозернистой структуры, массивной, реже грубополосчатой текстуры. Породообразующим минералом является кварц, содержание которого достигает 90-94%. Остальные минеральные материалы представлены мусковитом, биотитом, реже хлоритом, фукситом, альбитом, калиевым полевым шпатом.
Анализ результатов физикомеханических испытаний кварцитопесчаников Лебединского месторождения свидетельствуют об их высоком качестве. Средняя плотность — 2650 кг/м3, водопоглощение — 0,10%, пористость — 0,91%, временное сопротивление сжатию в водонасыщенном состоянии — 141,2 МПа, морозостойкость более 150 циклов, марка щебня по дробимости —1200, содержание серы в целом по месторождению (в пересчете на S03) — 0,18%.
В экспериментах применяли товарный цемент ЗАО «Белгородский цемент» марки ПЦ 500 ДО. Белгородская водопроводная вода имеет рН=7,12 (pH дистиллированной воды 6,5). Ее карбонатная жесткость составляет 5,5-5,6 Мг экв/ л. Практика использования стекловолокна для дисперсного армирования бетона показала, что, с точки зрения длительности сохранения армирующего качества, приемлемо волокно диаметром 13-15 мкм, чему соответствует использованный ровинг.
В качестве варьируемых параметров были приняты длина волокон (20, 35 и 50 мм) и процент армирования (1,5; 3,0 и 4,5) по массе при отношении цемента и песка 1:3. Выходными параметрами были средняя плотность стеклофибро- бетона (у), предел прочности при сжатии (RC)K), предел прочности на растяжение при изгибе (R), а также начальный модуль упругости.
Высушенные песок, цемент и стекловолокно смешивали до получения гомогенного состава, затем добавляли воду до образования однородной массы. После формования и уплотнения образцы находились под влажной мешковиной в течение 24 ч при температуре не выше 15°С. После расформовки бетонные кубики размером ребра 100 мм и призмы размером 120x120x400 мм помещали в камеру твердения с температурой 20°С и влажностью более 90%, что соответствует требованиям ГОСТ 18105.0-80 и 8829-85. Испытания образцов проводились на универсальной машине УМ-10 по стандартной методике (ГОСТ 10180-90), результаты представлены в таблице.
Анализ результатов испытаний кубов свидетельствует, что при введении стекловолокна в количестве 4,5% и более наблюдается тенденция к снижению предела прочности бетона при сжатии. При введении стекловолокна в количестве 1,5 и 3% с длиной волокон 20 и 35 мм отмечается повышение прочности бетона при сжатии (до 28%), а при увеличении длины волокна до 50 мм она имеет тенденцию к снижению.
Известно, что любые включения являются концентраторами напряжений, что в данном случае проявляется в значительной мере при длине стекловолокна свыше 35 мм и при увеличении процента армирования до 4,5%. Но в то же время оптимальная система включений способна притормозить, а в некоторых случаях и полностью остановить развитие трещин. Соответствующий анализ результатов испытаний призм показывает, что предел прочности бетона на растяжение при изгибе растет как при увеличении длины волокна, так и при росте процента армирования.
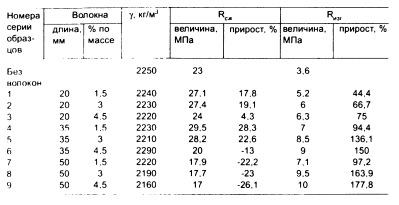
Жесткость пространственного каркаса из пленок вяжущего вещества обычно обусловлена его разновидностью. Жесткие перегородки кристаллизационного характера в мелкозернистом бетоне практически не реагируют на температуру окружающей среды. Включение стекловолокон делает перегородки подвижными, обладающими релаксационной способностью, что позволяет снять часть напряжений, возникающих в образце.
В ходе экспериментов проводились визуальные наблюдения за образованием и раскрытием трещин. Было установлено, что первые трещины появились при напряжениях от 20 до 30% от предела прочности на растяжение при изгибе. Они имели волосяной характер и закрывались при снятии нагрузки. Последние трещины при симметричном нагружении призмы образовывались симметрично относительно первичной трещины. Площадь поверхности трещинообраэования изменялась в зависимости от длины волокон и процента армирования.
Таким образом, полученные результаты свидетельствуют о том, что стекловолокно является эффективным дисперсным армирующим элементом для мелкозернистого бетона. С увеличением процентного содержания стекловолокон и их длины стабильно повышается прочность на растяжение при изгибе, что имеет немаловажное значение для повышения несущей способности конструкций, включающих изгибаемые элементы. Вместе с тем необходимо учитывать изменение предела прочности при сжатии и при осуществлении конкретных конструктивных решений находить оптимальные сочетания длины стекловолокна и процента дисперсного армирования мелкозернистого бетона.
Бетон и железобетон, 2006 №6