ШУГАЕВ В.В., СПАННУТЛ.С. Крупноразмерные железобетонные панели КЖС и перспективы их дальнейшего совершенствования
В конце 60-х годов в НИИЖБе по предложению видного ученого и инженера проф. Р.Н. Мацелинского была разработана сборная железобетонная предварительно напряженная конструкция покрытия, собираемая из панелей-оболочек КЖС[1].
Панель-оболочка решена по принципу короткого цилиндрического свода шириной 3 м, длиной 18- 30 м с двумя ребрами-диафрагмами сегментного очертания, в которых располагается предварительно напряженная арматура. Толщина поля панели-оболочки между ребрами - 30 мм. Объем бетона в панели длиной 18 м составлял 3,9 м3, а пролетом 24 м - 6,16 м3 при высоте панелей в ключе 1 и 1,3 м соответственно. Для устройства светоаэрационных фонарей в поле панели-оболочки могут быть выполнены круглые или прямоугольные отверстия размером до 2,5x9 м с соответствующим усилением поля панели вокруг отверстия. Панели-оболочки КЖС перекрывают пролет здания и укладываются на продольные несущие конструкции в виде балок или ферм, установленных на колонны продольных рядов (см. рисунок).
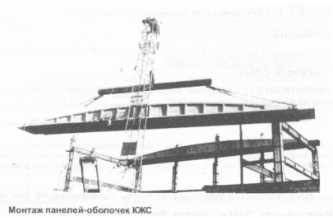
По указанию Госстроя СССР под руководством Р.Н. Мацелинского были выпущены типовые чертежи панелей пролетом 18 м (Проектный Институт ПИ-1) и пролетом 24 м (Харьковский ПромстройНИИпроект). Сравнительные техникоэкономические показатели покрытий из панелей КЖС и плоских плит по железобетонным стропильным фермам приведены в [2].
Общий объем применения в строительстве России покрытий промышленных и гражданских зданий с панелями-оболочками КЖС пролетом 18-30 м за прошедшие годы превысил 4,5 млн. м2.
Главным сдерживающим фактором расширения объема производства и применения панелей- оболочек КЖС в строительстве являлось непременное условие изготовления этих конструкций в заводских условиях. С одной стороны, это было оправданным с позиций повышения качества подобных ответственных конструкций и улучшения контроля за их изготовлением, но, с другой стороны, требовало затрат на транспортировку их к месту монтажа, на изготовление специальных автомобильных полуприцепов, дополнительную погрузку и разгрузку, организацию мест складирования на стройплощадках и главное - невозможность изменения габаритов и материала конструкции применительно к определенному снеговому району или конкретному зданию.
Еще при жизни Р.Н. Мацелинского его аспирантами и сотрудниками НИИЖВа были проведены многочисленные эксперименты и испытания натурных панелей КЖС с применением разновидностей тяжелого бетона (керамзитобетон и бетон на вулканическом шлаке Камчатки), различных отверстий в ребрах и плите. Кроме того, были выполнены расчеты и запроектированы панели с рабочей арматурой класса A-VI и разработаны своды пролетом 36 м из двух панелей пролетом 18 м, а в последние годы - большепролетные своды из трех и более панелей КЖС [5]. Все эти эксперименты, испытания и проектные работы были направлены на совершенствование конструкций покрытий и повышение их эффективности, но при изготовлении панелей-оболочек только в заводских условиях эго оказалось невозможным.
В связи с этим было бы правильным наряду с заводским изготовлением в большем объеме перейти к изготовлению панелей КЖС непосредственно на стройплощадке, в зоне действия монтажного крана. Прежде всего, это позволяет существенно облегчить форму- опалубку для изготовления конструкций. Все формы для заводского изготовления панелей были целиком стальными и рассчитывались по законам строительной механики так, чтобы обеспечивалась их прочность и жесткость при максимальном усилии натяжения рабочей арматуры панелей. Существующая ранее номенклатура стальных профилей была недостаточной для того, чтобы обеспечить необходимые требования по жесткости одних только нижних элементов формы, и поэтому в работу включалась стальная оболочка формы по всей длине, что увеличивало вес опалубки до 18 т при пролете 18 м и до 22 т - при пролете 24 м.
Для построечных условий рядом авторов в 1999 г. был предложен способ изготовления панелей [3], в котором усипие натяжения арматуры предлагалось передавать на нижние стальные профили, утопленные в бетонную подготовку пола строящегося здания, а остальные части опалубки (стальную оболочку и ребра) сделать съемными. Тогда после изготовления всех необходимых панелей для покрытия этого здания съемные детали можно было бы снять, а нижнюю часть опалубки залить бетоном, т.е. в стоимость формы при этом включается только нижняя часть опалубки. Можно предположить также, что при современном уровне развития техники верхнюю (съемную) часть опалубки в будущем заменит ПВХ достаточной прочности и жесткости, и это еще более снизит экономические и трудовые затраты на ее изготовление.
Здесь уместно сказать о некоторых недостатках заводского изготовления панелей, связанных с конструкцией форм и обычной технологией натяжения арматуры на всех заводах. Как уже отмечалось, ребра панелей имеют кессоны по всей длине, и во время прогрева панели температурное расширение стальных ребер формы опережает расширение бетона. Это часто вызывает появление волосных трещин на неармированных зонах ребер панели. Исследования показали, что эти трещины не влияют на прочность и несущую способность панели в целом, но их появление снижает эстетическое восприятие и вызывает при приемке панелей ненужные вопросы.
Авторы изобретения в 1989 г. предложили устройство для ликвидации таких трещин [4] с помощью применения магнитов в местах расположения кессонов и отделения последних от стальной оболочки опалубки.
Другой недостаток имеет более серьезное значение для несущей способности панелей. Он связан с технологией распалубки, при которой рабочую арматуру нагревают газовым резаком до появпения «шейки», после чего перерезают. При этом, как правило, происходит резкая передача усилия на одно ребро панели, а затем - на другое. В некоторых случаях при недостаточном наборе прочности бетона панели это может отрицательно повлиять на ее несущую способность. Чтобы предотвратить указанный недостаток, достаточно обеспечить плавную передачу усилия на оба ребра сразу с помощью специально разработанного и испытанного устройства на основе двух стальных вертикальных пластин с клиновой плоскостью с уклоном 1:10 и прорезью для арматуры.
Отказываясь от заводского изготовления-панелей, можно вносить различные полезные изменения в ее конструкцию: например, изменять размеры отверстий в ребрах, о которых сказано ранее, уменьшать высоты панели пролетом 24 м при некоторых сочетаниях нагрузок и даже при необходимости уменьшать габариты панели в плане. Последнее особенно важно для применения панелей в нестандартных производственных и гражданских зданиях. Предложенные мероприятия существенно улучшат качество панелей КЖС и расширят возможности их применения не только в производственных зданиях с крупными пролетами, но и в гражданских и сельскохозяйственных зданиях различного назначения.
К этому следует добавить соображения по применению стальных ферм с профилированным настилом поверху и сравнить их с панелями КЖС. Проведенное экономическое исследование зданий с пролетами 18 и 36 м и при длине пролетов 60 м показало, что применение панелей КЖС снижает стоимость «в деле» покрытия на 57% при пропетах 18 м, а по приведенным затратам - на 37%. При пролетах 36 м снижение стоимости составляет 35 и 27% соответственно. Кроме того, по некоторым прогнозам, сталь может существенно подорожать в ближайшие годы, и рост ее стоимости намного опередит рост стоимости цемента.
Ко всему сказанному можно добавить, что, отмечая высокий уровень производства монолитного железобетона на жилых и административных зданиях в Москве и в целом по России, наличие высококлассной отечественной и импортной техники, которая используется при выполнении большого объема монолитного домостроения, нет никаких сомнений в возможности реализации отмеченных технических и технологических новшеств при изготовлении панелей КЖС в зоне действия монтажного крана. При этом совсем не обязательно прогревать бетон в панелях традиционным паром, можно воспользоваться технологическими достижениями в области прогрева электрическим током (например, так называемым «греющим одеялом»). Для ускорения набора прочности можно применять различные высокоэффективные добавки с тем, чтобы добиться съема одной панели в сутки. Для защиты формуемых панелей от атмосферных осадков достаточно всю зону изготовления укрыть тентовым покрытием, допускающим возможность открывания какого-либо участка при подаче бетона в опалубку.
В прошлом году исполнилось 90 лет со дня рождения Р.Н.Мацелинского. Его замечательные идеи и предложения не забыты, они, несомненно, найдут применение при возобновлении производства и применения в строительстве пане- пей-оболочек КЖС на новом качественном уровне.
Бетон и железобетон, 2007 №2