МАЛИНИНА Л.А. К вопросу оценки эффективности цементов для тепловой обработки бетонов
Вопрос оценки и выбора цементов для бетонов, подвергаемых тепловой обработке (ТВО), являлся предметом многочисленных исследований. Эффективность цементов для ТВО ранее связывали с их маркой, вещественным и минералогическим составами. В нормативных документах по ТВО указывалось, что цементы должны быть алитовыми, тонкомолотыми, а по содержанию минерала С3А делиться на три группы: низко-, средне- и высокоалюминатные. Последние не рекомендовались для использования.
Необходимо отметить, что в СССР в связи с большими объемами производства сборного железобетона, в котором ТВО была неотъемлемым и самым длительным технологическим процессом, неоднократно ставился вопрос о производстве специальных цементов для ТВО бетонов. Однако эти требования не были реализованы.
В то же время при пересмотре стандартов на методы испытания цементов ГОСТом 310.4-76 было предусмотрено определение прочности цемента при пропаривании по стандартному режиму, которое действует и по сей день. Было установлено, что каждый цементный завод для выпускаемых им цементов имеет свою активность при пропаривании (Rft) и свой коэффициент эффективности, который определяется из формулы
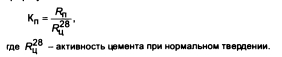
В настоящее время характеристики Rn и К,, являются информационными и указываются в качестве приложения.
В 80-х годах пошлого столетия ежегодно выпускался сборник «Качество продукции цементной промышленности СССР», в котором приводился комплекс сведений по каждому цементному заводу: минералогический и вещественный составы цемента, его активность при нормальном твердении в разном возрасте, активность цемента при пропаривании и др. Составителями этого сборника являлись Гипроцемент и НИИцемент.
Данные этих сборников были использованы аспирантом НИИЖБ А.Н.Мокрушиным в качестве первичного фактического материала для статистического анализа свойств цементов различных заводов СССР. Все цементы в зависимости от вещественного состава были разделены на 4 группы:
портландцементы без минеральных добавок (ПЦДО);
портландцементы с минеральными добавками (ПЦ-Д5 и ДОО);
быстротвердеющие портландцементы (БТЦ); шлакопортландцементы.
Анализ полученных статистических характеристик показал следующее. Средние значения активности цементов при пропаривании и коэффициентов эффективности при пропаривании не прямо пропорциональны марке даже для одного вида и близкого минералогического состава цемента. На одних цементных заводах высокой марке цемента могут соответствовать низкие значения активности и коэффициента эффективности при пропаривании; на других заводах, наоборот, низкой марке цемента - высокие значения активности и коэффициента эффективности при пропаривании.
Цементы разных видов (например, БТЦ и ШПЦ) при одной и той же марке, но изготовленные на разных заводах, могут иметь близкие или даже одинаковые значения активности и коэффициента эффективности при пропаривании. Активность при пропаривании и коэффициент эффективности при пропаривании изменяются по заводам страны почти в два раза даже для цементов одного вида и марки - от 18 до 41 МПа, а коэффициент эффективности при пропаривании - от 0,40 до 0,86 [1,2]. Приведенные данные свидетельствуют о том, что между активностью цемента при пропаривании и активностью при нормальном твердении нет единой, достаточно тесной, корреляционной зависимости.
Важным результатом анализа является вывод о том, что среднегодовые значения коэффициента эффективности при пропаривании для конкретного за- вода-изготовителя являются величиной, мало изменяющейся во времени и незначительно зависящей от марочности цементов и их вещественного состава. Внутризаводской коэффициент вариации коэффициента эффективности при пропаривании изменяется от 2 до 8% для цементов одного вида и марки.
На основании этих исследований все цементы, выпускаемые по ГОСТ 10178-85, были классифицированы на три группы:
высокоэффективные, I группа, > 0,68; среднеэффективные, II группа, kj, = 0,57-0,68; низкоэффективные, III группа, Кп < 0,56. Применение низкоэффективных цементов III группы требует существенного увеличения расхода цемента (до 50 кг/м3) при требуемых показателях отпускной или передаточной прочности бетона или же существенного повышения длительности тепловой обработки. Объем производства цементов в среднем в СССР составлял: высокоэффективных - 36%, среднеэффективных - 41%, низкоэффективных - 23% от общего объема выпускаемых цементов. Эти данные полностью согласуются с прямыми экспериментами на бетонах различных марок, подвергаемых ТВО при температурах 85,60 и 50°С, и отражены в различных нормативных документах и публикациях.
Установить причины столь неоднозначного поведения цементов при твердении практически одинакового расчетного минералогического состава пытались многие известные ученые ещё в 30-х годах прошлого века. В.Н. Юнг [3] писал, что, кроме основных соединений, по которым ведется расчет минералогического состава клинкера, в сырье содержится более 2% второстепенных веществ. К ним относятся щелочные окиси, двуокиси титана, окиси марганца, фосфаты и др. В последующие годы о влиянии малых примесей в цементной шихте на формирование минералов клинкера и их свойства указывали Ю.М. Бутт, В.В. Тима- шев, Ю.С. Малинин и др.
К числу фундаментальных исследований этого вопроса с применением самых современных инструментальных методов следует отнести работы, проводимые в течение многих лет в институте химии силикатов РАН д.х.н., профессором А.И. Байковой [4, 5].
По её данным, в исходных клинкерных композициях, составляемых из природных материалов (известняка, глины) и техногенных отходов различных производств (шлаков, зол и др.), всегда присутствуют до 12-15 элементов. Лишь четыре из них - Са, Al, Fe, Si
- образуют с кислородом матричные соединения, являющиеся основой реальных клинкерных фаз - элита, белита, алюмината и алюмоферрита. Примесные элементы, которые часто называются «второстепенными», играют неоценимую роль в процессе клинке- рообразования. Так, если бы цемент состоял только из чистых силикатов C3S и C2S, то температура его обжига должна быть порядка 2000‘С. Лишь присутствие в сырьевой шихте примесных компонентов (Na, К, Mg, Zn, Sr, Ва, Al, Fe, Cr, Ti, P, S и вероятных других) делают возможным вести обжиг клинкера в промышленных условиях при более низких температурах (- 1450°С). Поскольку примеси остаются в многофазной клинкерной системе, неизбежна проблема их взаимодействия с матричными соединениями. Однако каждое из последних может разместить в своей кристаллической решётке лишь определенное количество примесей. Наибольшее их количество сосредоточивается в алюминатной и алюмоферритной фазах, а наименьшее - в структуре C3S (алите). Группы главных и второстепенных (в скобках) изоморфных примесей в матричных соединениях следующие [4]:
3Ca0Si02 - Mg, Al, Fe (Na, К, Cr, Ti, P, S и др.);
2Ca0Si02 - К, Mg, Al, Fe, P, S (Na, Mn, Cr и др.);
4CaOAI203Fe203 - Mn, Mg, Ti, Si (Na, K, Cr и др.);
3Ca0AI203 - Na, К, Fe, Si (Mg, Mn, Cr, Ti, и др.).
Эти данные свидетельствуют о том, что наличие примесей в структурах реальных клинкерных фаз приводит к несоответствию расчетного и фактического содержания их в клинкере, так как количественный минералогический состав клинкера, как правило, определяется исходя из «чистых» (матричных) соединении C3S, C2S, С3А, C4AF.
Количество и набор примесей в цементной шихте может изменяться при разработке новых месторождений, а также при использовании различных техногенных отходов, особенно таких, как шлаки и золы, содержащих большой набор микроэлементов и являющихся полноправными участниками формирования клинкерных фаз. К сожалению, следует отметить недостаточность исследований в этом направлении вследствие их большой сложности. Практически отсутствуют данные о влиянии вида микропримесных соединений на гидравлическую активность цементов, особенно при их твердении при различных температурах. Поэтому при оценке эффективности цементов для тепловой обработки бетонов при температурах до 100°С единственно приемлемыми являются прямые методы оценки их гидравлической активности при испытании по ГОСТ 310.481 с последующим делением их на три группы, которые приведены в ГОСТ 10178.85. В соответствии с ГОСТ 30515-97 (приложение Д) каждый цементный завод должен давать документ на поставляемый цемент, в мотором приводится его средняя активность при пропаривании.
В настоящее время в нашей стране действуют два стандарта на цементы: ГОСТ 10178.85 (ТУ) и ГОСТ 310.481 на методы испытаний, а также новый ГОСТ 31108-2003 (ТУ) и ГОСТ 30744-2001 на методы испытаний, гармонизированные с Евростандартами EN 197-1 и EN 196. В этих ГОСТах отсутствуют какие- либо сведения об активности цемента при тепловой обработке - очень важная для строителей России характеристика цемента, так как весь сборный, а также и монолитный бетоны, подвергаются различным видам ТВО.
Бетон и железобетон, 2007 №4