А.А. КВАСНИКОВ, инж., А.С. СЕМЧЕНКОВ, д-р техн.наук (НИИЖБ); С.К. МАКАРЕНКО, канд. техн.наук (КиевЗНИИЭП), АНАЛИЗ ЭКСПЕРИМЕНТАЛЬНО-ТЕОРЕТИЧЕСКИХ ИССЛЕДОВАНИЙ НА СДВИГ СОПРЯЖЕНИЙ СБОРНЫХ ПЕРЕКРЫТИЙ
Сборный диск перекрытия связевого каркаса, состоящий из плит и ригелей, представляет собой наиболее материалоемкий элемент, на который приходится до 50% бетона и стали, идущих на здание. Пространственная жесткость сборного диска обеспечивается за счет сварки закладных деталей и омоноличивания шпоночных сопряжений между элементами диска. Сопряжения препятствуют взаимным смещениям соседних элементов диска и заставляют их деформироваться совместно, превращая в пространственный диск перекрытия.
В строительной практике за рубежом широко использовались плиты перекрытия типа 2Т. В нашей стране такие плиты первоначально пытались применять в покрытиях одноэтажных промышленных зданий. Однако распространения они не получили из-за малого расстояния между ребрами (1,5 м), что вызывало дополнительные усилия в верхнем поясе стропильных ферм, а также из-за неуверенности проектировщиков в надежности сопряжений между консольными свесами плит при горизонтальных крановых нагрузках [1]. В свое время плиты 2Т были включены в состав всесоюзной серии 1.020-1/88 межвидового применения и Московского каркаса ТК1-2, том 1; при этом толщина полок вдоль межплитных швов была увеличена с 3 до 5...6 см, что повысило надежность этих сопряжений [2].
Основной недостаток дисков из плит 2Т в составе связевых каркасов заключается в большом количестве конструктивных закладных деталей, устанавливаемых без расчета между плитами и плитами и ригелями. Отсутствие экспериментальных данных до сих пор не позволяло выявить действительную картину напряженно-деформированного состояния дисков перекрытия и их сопряжений, установить имеющиеся резервы прочности и жесткости и уточнить методы расчета.
В данной работе приведены результаты испытаний на сдвиг комплексных сопряжений между консольными свесами плит 2Т и Т, а также сопряжений с прерывистыми шпонками.
Опытные образцы комплексных сопряжений собирали из трех армированных проволочными сетками плит из бетона прочностью 50 МПа, толщиной 50 мм. В испытаниях ставилась задача исследовать влияние конструктивных связей и ширины шва (5Ш) в сопряжении на его прочность и деформативность при сдвиге в горизонтальной и вертикальной плоскостях. Для обоих видов испытаний было изготовлено по две серии из трех образцов в каждой. Ширина швов 5 в 1-й серии была 20, во 2-й - 40 мм. В образцах № 1 плиты соединялись приваркой металлических пластин размером 100х90х5 мм к закладным деталям в виде уголков (рис.1); в образцах № 2 - дополнительно омоноличивали мелкозернистым бетоном прочностью 7,5 МПа шпонки размером 150х50х20 мм, а в образцах № 3 - еще и швы по всей длине.
В принятой маркировке образцов СТ-3в-20, СТ-3г-20 первая цифра 3 указывает номер образца в серии, буквы в и г - вид нагрузки (вертикальная и горизонтальная), а последние две цифры означают ширину швов в мм. Деформации сдвига замерялись индикаторами часового типа, которые устанавливались по две штуки вдоль сопряжения (рис.1, а, в).
Комплексные сопряжения испытывались на сдвиг в плоскости диска на прессе при вертикальном положении образцов. Нагрузка от домкрата прикладывалась к верху средней плиты через катки, установленные возле швов, опорные катки ставили снизу в крайних плитах возле швов (рис.1, в). Нагрузки на домкрат увеличивали, и замеряли соответствующие им деформации (рис.2), поэтому удалось получить лишь восходящие участки диаграмм. В результате усреднения показаний четырех индикаторов получены диаграммы, имеющие упруго-пластический характер. Разрушение образцов происходило при достижении максимальной нагрузки S и росте пластических деформаций более 3...5 мм, замерить которые ввиду несовершенства нагружающего и измеряющего оборудования не удалось (рис.2, а, б).
Первые трещины в образцах № 1, объединенных накладками, возникали у нижних закладных деталей при нагрузках 0,5...0,8 разрушающей S. При нагрузках 0,85...0,9S деформации начинали интенсивно нарастать, ширина каждой из трещин превышала 1,5...2 мм, и при дальнейшем загружении бетон возле закладных деталей разрушался (рис.1, д) при нагрузках 160 и 140 кН соответственно в образце с 5 = 20 мм и 40 мм.
В образцах № 2 и № 3 первые трещины появились по линии контакта бетона шпонок и плит при нагрузке около 0,35S. Далее в образцах № 2 при нагрузке 0,8S образовались трещины в бетоне плит возле закладных деталей. Сопряжения разрушались в результате одновременного раскалывания шпонок по сжатым полосам выкалывания бетона плит закладных деталей и продергивания их анкеров из-за малой толщины полок при нагрузках 185 и 165 кН, соответственно, при 5 = 20 мм и 40 мм. Трещины в омоноличенных швах образцов № 3 появлялись при нагрузках 0,4...0,6S, а при нагрузках 0,75...0,85S - в плитах. Разрушение образцов сопровождалось одновременным сколом шпонок по сжатой диагонали, смятием и сдвигом бетона шва, а также разрывом бетона плит у закладных деталей и происходило при нагрузках 230 и 200 кН соответственно, при 5 = 20 мм и 40 мм. (рис.1, д, 2, а).
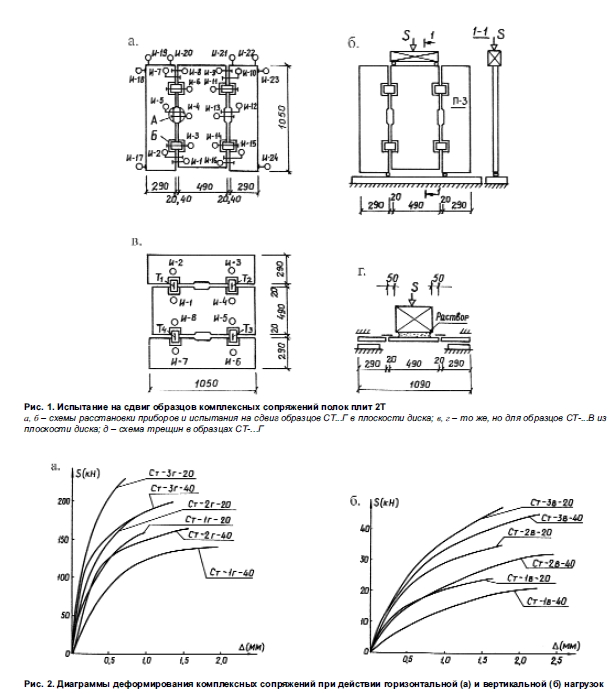
Таким образом, увеличение вдвое толщины шва снизило прочность всех трех видов образцов всего на 11...13%; это неопасно и может не учитываться в расчетах. При обеих толщинах швов омоноличивание шпонок повысило прочность сопряжений на 16...18%, а омоноличивание шпонок и швов - на 43...44%. Поскольку в типовых плитах закладные детали в консолях полок устанавливаются с интервалом 1,5 м, прочность сопряжений при длине 12 м, 5 = 40 мм и даже при отсутствии омоноличивания составляет 315 кН, что значительно больше допустимого сдвигающего усилия в плоскости диска, равного 80 кН.
При сдвиге швов на 0,5 мм дополнительные связи в них больше увеличивают жесткость в сопряжениях с более широкими швами. Увеличение в два раза ширины швов снижает жесткость сопряжения в среднем на 25% (19...33%). При наличии только закладных деталей жесткость сопряжения на два порядка ниже жесткости на сдвиг полки плиты из бетона класса В20. Поэтому, как показали испытания фрагментов дисков перекрытия, омоноличивание сопряжений первого типа желательно, так как в этом случае сборный настил работает, как цельная балка, и взаимного сдвига плит вдоль сопряжений не происходит. Поэтому дополнительная монолитная стяжка под полы толщиной 6 см по поверхности настила из плит 2Т не оказывает влияния на работу диска перекрытия в своей плоскости [2] и, следовательно, не нужна.
Комплексные сопряжения на сдвиг в вертикальной плоскости испытывали в специальном стенде, располагая опытные образцы горизонтально. Крайние плиты защемлялись с помощью траверс и тяг, крепящихся в силовом полу. Вертикальная нагрузка от домкрата передавалась на среднюю плиту сверху через жесткий штамп (рис.1, г). Диаграммы деформаций стыков имеют упруго-пластический характер. Наибольшие замеренные при испытаниях деформации сдвига во всех сопряжениях превышали 2 мм (рис.2, б). Прочность сопряжений, объединенных только закладными деталями, составила 23 и 20 кН, а жесткость при сдвиге А = 1 мм - 20,7 и 13,8 кН/мм, соответственно при 5 = 20 мм и 40 мм (рис.2, б).
Образцы разрушались по бетону шпонок, швов и плит возле закладных деталей (рис.1, д). Омоноличивание шпонок и целиком сопряжений привело к увеличению прочности сопряжений соответственно в 1,52.1,55 и 2,09.2,20 раза, а жесткости - в 1,44...1,82 и 1,77...2,43 раза, причем меньшие значения относятся к образцам со швами шириной 20 мм. Следовательно, более чувствительными к заделке сопряжений оказались более широкие швы. Увеличение ширины швов снизило прочность на 8...13%, а жесткость - на 8...33% (меньшие значения относятся к неомоноличенным, а большие - к полностью омоноличенным сопряжениям). Значения разрушающих нагрузок сопряжений в вертикальной плоскости оказались в 5...8 раз, а жесткостей - в 4,7...6,2 раза ниже, чем в горизонтальной (рис.2, а, б).
Образцы СТ-1г-0 и СТ-1в-0 были испытаны при нулевом зазоре в швах. В результате прочность сопряжений увеличилась и составила соответственно 219 и 38 кН. При испытании в вертикальной плоскости произошло зажатие швов от изгиба средней плиты, в них возникло обжатие от моментной пары, и образец стал работать аналогично испытанию омоноличенными сопряжениями.
Следует отметить, что закладные детали в сопряжениях плит типа Т и 2Т, учитывая их большое количество, достаточно материалоемкие - на них приходится 5...20% всего расхода стали на плиту. Поэтому, стремясь сократить их количество, необходимо также вести поиск облегченных конструктивных решений. В связи с этим были проведены испытания двух усовершенствованных конструкций стыков на аналогичных образцах без омоноличивания сопряжений. Ширина швов в образцах была равна 10 мм.
В отличие от типовых деталей, в новых вместо уголка применена накладная пластина, которая анкеруется в полке в одном случае гнутой П-образной шпилькой, привариваемой ручной дуговой сваркой, а в другом - укороченными стержнями, привариваемыми автоматической сваркой и имеющими высаженные головки по концам. Между собой закладные детали соединяются с помощью пластин или арматурными коротышами. Оба новых стыка по расходу стали на 17 и 40% экономичнее типовых. Прочность образцов в горизонтальной плоскости составила 246 и 216 кН, т. е. близка к типовым сопряжениям с омоно- личенными швами, но их жесткость (162 и 130 кН/мм) значительно ниже, чем даже в типовых сопряжениях с неомоноличенными швами, что объясняется их конструктивными особенностями. В вертикальной плоскости прочность сопряжений составила 40,5 и 35,8 кН.
Теоретически затруднительно определить гарантированную границу между шпонками смятия, разрушающимися пластически при больших деформациях, и шпонками среза, разрушающимися хрупко. Поэтому цель данных испытаний шпоночных сопряжений заключалась в определении размеров шпонок, исключающих их хрупкое разрушение при различной толщине шва и величине бокового обжатия.
Образцы состояли из трех призм с двумя шпонками в каждом шве (рис.3). Шпонки омоноличивали мелкозернистым бетоном прочностью 7,5 МПа. Испытания проводились в прессе, нагрузка прикладывалась к средней призме, а крайние упирались в нижнюю плиту пресса через катки, устанавливаемые по граням швов, чтобы максимально приблизиться к сдвиговой схеме. Для объединения призм использовали рамки, которые с помощью болтов создавали также боковое обжатие, замеряемое динамометрами сжатия (рис.3, г).
Призмы образцов формовали в деревянной опалубке из бетона прочностью 40 МПа и армировали сетками из проволоки класса Вр-1. Были изготовлены два вида образцов (рис.3, б, в) с различной высотой шпонок (140 и 220 см), условно маркированные, соответственно, СТП (стыки межплитные) и СТР (стыки между ригелями и плитами).
Глубина шпонок во всех образцах была 20 мм, а длина равнялась толщине призм - 100 мм. Для обоих видов шпоночных сопряжений было изготовлено по три серии образцов, отличавшихся толщиной швов. Для первого вида сопряжений ширина швов составила 0,20 и 40 мм. Во втором виде сопряжений - соответственно 0,10 и 20 мм. Каждая серия содержала по четыре образца, отличающихся величиной бокового обжатия швов, одинаковой для обоих видов образцов и равной 0, 10, 50 и 100 кН.
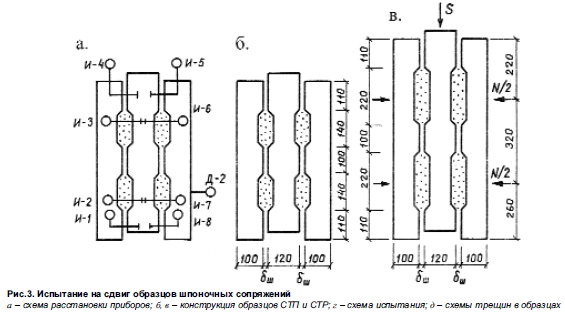
В полной маркировке образцов - СТП-2-20-1 - первая цифра обозначает порядковый номер образца в серии, вторая - ширину швов в мм, а третья - усилие обжатия в тс.
Первыми во всех образцах марок СТП и СТР открывались трещины по линии контакта нижних шпонок при нагрузке 0,33...0,6 от разрушающей, причем меньшая нагрузка относится к образцам без бокового обжатия, а большая - с обжатием 100 кН. В верхних шпонках контактные трещины открывались на 1...2 ступени позже. Ширина швов практически не повлияла на относительную величину нагрузки, вызвавшей образование трещин. Деформации сдвига швов до разрушающей величины 0,35...0,4 были близки к линейной, а при увеличении нагрузки начинали интенсивно нарастать неупругие деформации (рис.4, а, б). Максимальные деформации сдвига в момент перед разрушением образцов замерить не удавалось из-за их интенсивного нарастания под нагрузкой. Поэтому на диаграммах показаны значения лишь начальных деформаций на последнем этапе, которые составляли в среднем 1...2 мм в не- обжатых швах и 0,5 мм в обжатых. Раскрытие швов в необжатых образцах достигало перед разрушением 2 мм при 5 = 0 мм и 4 мм при раздвинутых швах. В обжатых образцах поперечные деформации швов не достигали 0,5 мм.
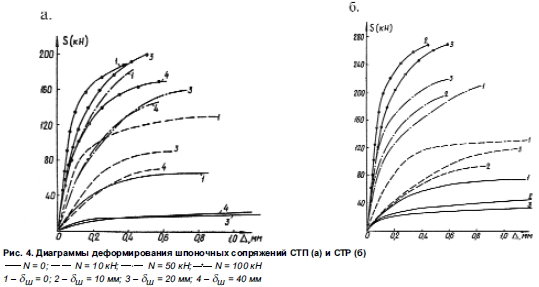
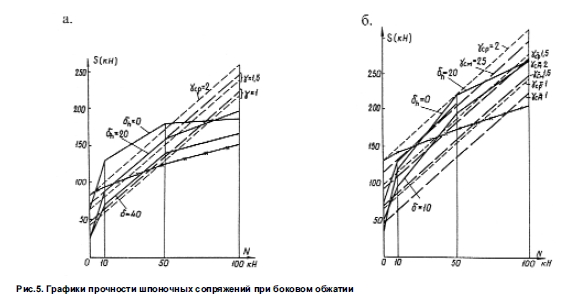
Прочность сопряжений в значительной степени зависела от величины бокового обжатия и ширины шва. Разрушение обоих видов образцов с раздвинутыми на 20...40 мм швами при отсутствии обжатия происходило при низких значениях нагрузки в результате местного смятия сжатых углов шпонок и раздвижки образцов. При этом бетон шпонок был цел, и в нем даже отсутствовали трещины. Все остальные образцы разрушились в результате раскалывания бетона шпонок трещинами, идущими вдоль сжатых полос (рис.3, д). При этом в образцах СТР с более высокими шпонками сжатые полосы шпонок в углах были обмяты, и трещины среза появлялись при разрушении фрагмента и больших деформациях сдвига, замерить которые не удалось.
Из графиков прочности сопряжений (рис.5), построенных по результатам испытаний, видно, что влияние бокового обжатия на прочность сопряжения зависит от ряда факторов: при увеличении обжатия снижаются его влияние и влияние ширины шва; обжатие оказывает более существенное влияние в образцах с высокой шпонкой. Следует отметить заметный разброс опытных значений прочности сопряжений.
Теоретические кривые прочности сопряжений (рис.5, а, б) построены по формулам (1), (2), аналогичным формуле Кулона
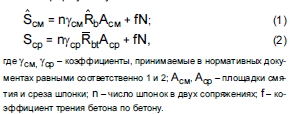
В формулах (1), (2) разные авторы используют различные значения коэффициента уср, принимая его равным 1,5 [3] и п/2 [4], а усм - 1,5 [3].
На рис.5 приведены также кривые, построенные по формуле полученной на основе теории Друккера при уср = 2.
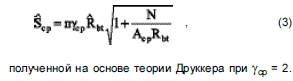
Из сравнения теоретических кривых следует: формула (3) имеет худшую сходимость с экспериментом, чем формулы (1) и (2); увеличение толщины швов заметно снижает прочность образцов СПТ и слабо влияет на прочность образцов СТР с более высокой шпонкой; криволинейность графиков указывает на снижение величины коэффициента трения при больших значениях обжатия шпонок; при коэффициенте уср = 2, как правило, имеет место завышение теоретического значения прочности, что указывает на разрушение шпонок от смятия.
На основании анализа результатов испытаний рекомендуется при расчете шпонок по формулам (1) и (2) по 1-й группе предельных состояний принимать Уср = 1,5 Усм = 1 a по 2-й группе - Уср = 2 Усм = 1,5 Отношение размеров hh/5h шпонок следует принимать не менее 7, чтобы исключить хрупкое разрушение шпоночных сопряжений от среза.
Бетон и железобетон, 2008 №1