Б.Д. ТОТУРБИЕВ, академик РИА, д-р техн. наук, проф., А.Б. ТОТУРБИЕВ, канд. техн. наук, ВЯЖУЩИЕ ИЗ ОБОЖЖЕННЫХ ГЛИНИСТЫХ СЛАНЦЕВ
Одним из основных направлений развития технологии производства цемента является расширение выпуска многокомпонентных высококачественных и специальных цементов на основе портландцементного клинкера и различных добавок, что дает возможность не только снизить энергозатраты, но и получать цементы с принципиально новыми свойствами.
В данной статье приводятся результаты исследования, направленные на обеспечение возможности использования обожжённых глинистых сланцев в производстве бесклинкерного известкового вяжущего, тонкомолотых пуццолановых портландцементов (ППЦ) и вяжущих низкой водопотребности. При этом рассматривалась также возможность использования глинистого сланца как сырьевого компонента при производстве портландцементного клинкера.
Используемый глинистый сланец Дагестанского месторождения представляет собой смесь глинистых минералов: хлорита, монтмориллонит - гидрослюдистого смешано-слойного образования, полевых шпатов, гидрооксидов железа и кристаллического кварца. Химический состав глинистого сланца приведён в табл. 1, откуда следует, что исходный материал в основном содержит оксиды кремния, алюминия и железа, а оксиды кальция и магния представлены в незначительном количестве. Потери при прокаливании (9,6%), видимо, определяются дегидратацией глинистых минералов, а также выгоранием органики.
Для определения возможности использования глинистого сланца в производстве вяжущих веществ проведён радиационный анализ, в результате которого установлено, что в указанном исходном материале содержание естественных радионуклидов, выраженное величиной удельной эффективной активности, не превышает порогового значения в 370 Бк/кг. Данный материал, по классификации РКСМ, относится по виду использования к 1 классу (использование без ограничений), имеется сертификат РКСМ.
Проведённые дифференциально-термический, рентгенографический и петрографический анализы глинистого сланца показали, что его разложение происходит при температурах 465-5500С. При этих же температурах на рентгенограмме отмечается частичное разложение хлорита с образованием гематита, количество которого с увеличением температуры растёт, что отмечается красной окраской полученного продукта при обжиге. На рентгенограмме имеются также линии, относящиеся к минералу монтмориллониту. Дифферинциально-термическим анализом установлено удаление адсорбированной воды при 100-1900С, конституционной при 500-6000С и разрушение кристаллической решетки при температуре 800-8800С. В этом интервале температур (8008800С), по данным петрографического анализа, отмечается образование стеклофазы. При температуре 12500С происходит полное разложение глинистых минералов и кварца с образованием муллита и гематита, а также увеличивается количество стеклофазы. Таким образом, на основании комплексных физико-химических исследований можно отметить, что представленное вещество (глинистый сланец) после обжига не может обладать гидравлической активностью без соответствующих добавок.

Проведенные расчёты показали, что необходимая по химическому составу сырьевая смесь для получения портландцементного клинкера может быть составлена только из четырёх компонентов, % по массе: глинистый сланец - 18, известняк - 77, железистые огарки - 1.8, кварцевый песок - 3.6. Однако применение такого состава при производстве портландцементного клинкера усложнит схему первичной переработки и шихтовки, что, в свою очередь, повысит себестоимость продукции. Поэтому в дальнейшем наши исследования были направлены на использование обожженных глинистых сланцев в качестве активной минеральной добавки для приготовления известково-пуццоланового вяжущего, а также при помоле клинкера с получением портландцемента (до 20%), либо пуццоланового цемента (до 40% добавки).
Этот вариант для Северо-Кавказского региона, в частности для Дагестана, является наиболее целесообразным, так как в городе Махачкале завершается строительство помольного цеха мощностью 500 тыс. т. портландцемента в год на основе клинкера Шалинского или Карачаево-Черкесского цементного заводов. При этом введение различных местных добавок обеспечит минимальные затраты и обеспечит высокую окупаемость продукции.
Для предварительной оценки возможности приготовления из представленного материала активной минеральной добавки была проведена серия обжигов исходного сырья при температурах 550, 800 и 12500С. Выдержка минерала в обжиговой печи при заданной температуре была принята во всех режимах 1 ч. Для получения сравнительной оценки гидравлической активности материала, полученного при каждом из обжигов, были изготовлены образцы из обожжённого материала в виде кубиков размером 1х1х1 см. Составы, из которых изготовлены образцы, отличались по соотношению цемента и добавки 1:4 и 1:1 (см. табл. 2).
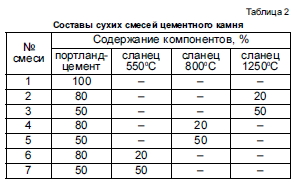
Образцы изготавливались из цементного теста (без песка). Формы с образцами выдерживали 1 сут во влажной среде, а затем расформовывали и помещали в ванну с водой. Испытания прочности на сжатие проводились на ручном прессе через 3, 7, 14, 21 и 28 сут. В каждом определении разрушению подвергались 6 кубиков. Результаты испытаний (в МПа) представлены в табл. 3, откуда следует, что наилучшие показатели по прочности имеют образцы, изготовленные на основе добавки, обожжённой при температуре 8000С, при соотношении добавки и цемента 1:4.
Близкие результаты показывает добавка, обожжённая при температуре 5500С. Обжиг при температуре 12500С приводит к ухудшению показателей. Таким образом, результаты проведенных испытаний позволяют сделать предварительный вывод о возможности получения активной минеральной добавки на базе глинистого сланца Дагестанского месторождения путём обжига при температуре 550-8000С. Указанная добавка может быть использована при совместном помоле с портландцементом или портландцементным клинкером в количестве не менее 20% по массе.
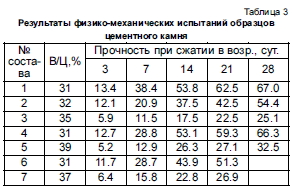
Предварительные результаты, полученные на образцах цементного камня с введением обожжённого (8000С) глинистого сланца, были уточнены при испытании различных видов вяжущих по стандартным методикам, в том числе с определением нормальной густоты, сроков схватывания, нормальной консистенции стандартных растворов состава 1:3 и их активности как при нормальном твердении, так и при тепловлажностной обработке (ТВО) по режиму 2+3+6+2 ч при температуре изотермического прогрева 85-900С (методики ГОСТ 310.1-76...310.3-76, 310.4-81).
Изготовлению вяжущих предшествовала соответствующая подготовка сырьевых материалов: предварительное измельчение извести и гипсового камня в щековой дробилке и предварительный помол портландцементного клинкера и обожжённого сланца в шаровой мельнице. Дисперсность полученной после одновременного помола крупки портландцементного клинкера соответствовала удельной поверхности около 1500 см2/г, обожжённого сланца - 4500-5000 см2/г, что подтверждает его высокую размолоспособность.
Приготовление вяжущих осуществлялось в лабораторной мельнице совместным помолом компонентов. Продолжительность помола корректировали с учётом интенсифицирующего воздействия добавки С-3 и повышенной размолоспособности обожжённого сланца и извести. Испытания проводились с использованием алитового клинкера среднего минералогического состава, гипсового камня (двуводный сульфат кальция), полуводного (строительного) гипса и извести. Данные по вещественному составу вяжущих, значения их удельной поверхности и показатели плотности приведены в табл. 4. Полученные результаты показывают, что наименьшими показателями плотности характеризуется известковое вяжущее, что соответствует более низкой плотности его компонентов - извести и сланца.
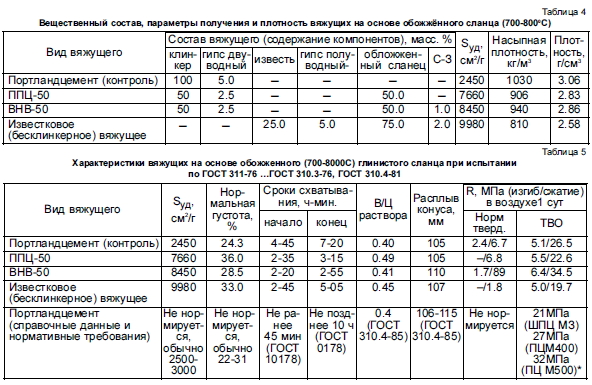
Результаты определения стандартных характеристик полученных вяжущих приведены в табл. 5. Они свидетельствуют о более высокой водопотреб- ности вяжущих, содержащих обожженный сланец, нормальная густота которых (28.5-36%) существенно превышает водопотребность контрольного портландцемента (24.3%). Наибольшей водопотребностью отличается вяжущее ППЦ-50 (36%), несколько меньшей (33%)- известковое вяжущее. Наименьшее значение нормальной густоты (28.5%) характерно для ВНВ-50. Оно же отличается наиболее сокращёнными сроками схватывания, причём ускоренное структуро-образование теста на ВНВ-50 является косвенным показателем интенсивности твердения вяжущего. Наиболее длительными сроками схватывания обладает бесклинкерное известковое вяжущее, структурообразование которого на ранней стадии в значительной степени определяется гидратацией полуводного гипса, количество которого сравнительно невелико.
Водопотребность растворов нормальной консистенции в целом соответствует водопотребности теста на различных вяжущих. В то же время следует отметить практически равную потребность растворов на портландцементе и ВНВ-50, несмотря на несколько повышенную нормальную густоту последнего. Это связано с особенностями реологических свойств бетонных и растворных смесей на основе вяжущих низкой водопотребности, а именно, их повышенной способностью к тиксотропному разжижению в условиях механических воздействий.
В возрасте 1 сут как нормального твердения, так и после ТВО наибольшими прочностными характеристиками отличаются растворы на ВНВ-50. При нормальном твердении их прочность при сжатии составила 8.9 МПа, а после тепловлажностной обработки - 34.5 МПа, что на 33 и 30% выше соответствующих значений прочности контрольных образцов на портландцементе. Прочность при сжатии образцов нормального твердения на ППЦ-50 практически не отличается от прочности контрольных образцов, а при использовании известкового вяжущего значения прочности почти в 4 раза ниже. При этом образцы нормального твердения как на ППЦ-50, так и на известковом вяжущем практически не имели прочности при изгибе.
В условиях тепловлажностной обработки гидратационные процессы в известковом вяжущем значительно интенсифицируется, а прочность составляет 19.7 МПа, уступая прочности контрольных образцов не более чем на 26%. Прочность пропаренных образцов на ППЦ-50 была ниже контрольных на 15%.
Во всех случаях использования вяжущих на основе сланцев пропаренные образцы не имели признаков деструктивных изменений (трещин, вспучивания поверхности), что подтверждает выражаемые сроками схватывания данные об их достаточно интенсивном структурообразовании в первые часы после затворения.
Бетон и железобетон, 2008 №1